Computational Design is generating increasing interest in the construction industry as well as a certain amount of confusion. It is not parametric design; instead it takes parametric design to the next level. It is a set of methods that will define how we design structures over the next decades.
With Computational Design, you don’t design the building; you design the automated process to find the best building design.
To learn more about computational design, please refer to the chapter “Advanced Applications in Computational Design” by the author with Paul Jeffries, Alex Christodoulou, Rick Titulaer, Paul Shepherd, Sean Lineham, Hannah Lazenby, Stephen Melville, and James Solly, as part of a Springer book Industry 4.0 for the Built Environment, edited by Marzia Bolpagni, Rui Gavina, and Diogo Rodrigo Ribeiro.
Why use Computational Design?
Computational Design is enabling us to create buildings that are far more efficient than we can manage using more traditional methods. Some architects are indeed using it to produce novel building forms, but its great advantage is in helping us towards efficient, zero-carbon construction.
How do you use Computational Design?
In traditional building design, numerous decisions are made early in the process, such as structural type, column spacing, and floor-to-floor heights, either by experience or by tables in scheme design guides. The detailed design then makes the layout work, determining section sizes, reinforcement layouts, and details, though design development across the team can lead to costly changes to the scheme.
With Parametric Design, the design is driven by algorithms controlled by the designers so that the team can explore values such as column spacing. Parametric Design also allows the use of more complex geometry so that, for example, the architect might define the facade using a spline surface. The engineer then sets up rules to offset this to allow for the cladding thickness, adds rules for maximum purlin spacing, and so on, automatically generating the structural layout.
Computational Design is Parametric Design but with the assessment of the quality of the design calculated automatically, whether least weight, material usage, embodied carbon, or maximising sunlight. This quality assessment is fed back into the algorithms, automatically adjusting the input values until the quality is maximised.
This “quality” of design is a set of criteria determined by the design team and can take many forms, as we will see below. This means that the team generates the final design by controlling the definition of the output required and the algorithms used to achieve it, enabling their Computational Design system to search for ideal, or at least, better design solutions than they might have the time or intuition to find using more traditional techniques.
What results does Computational Design give?
You can apply Computational Design at any stage in a project, here are just a few examples.
Transport for London Mass Land Viability Study
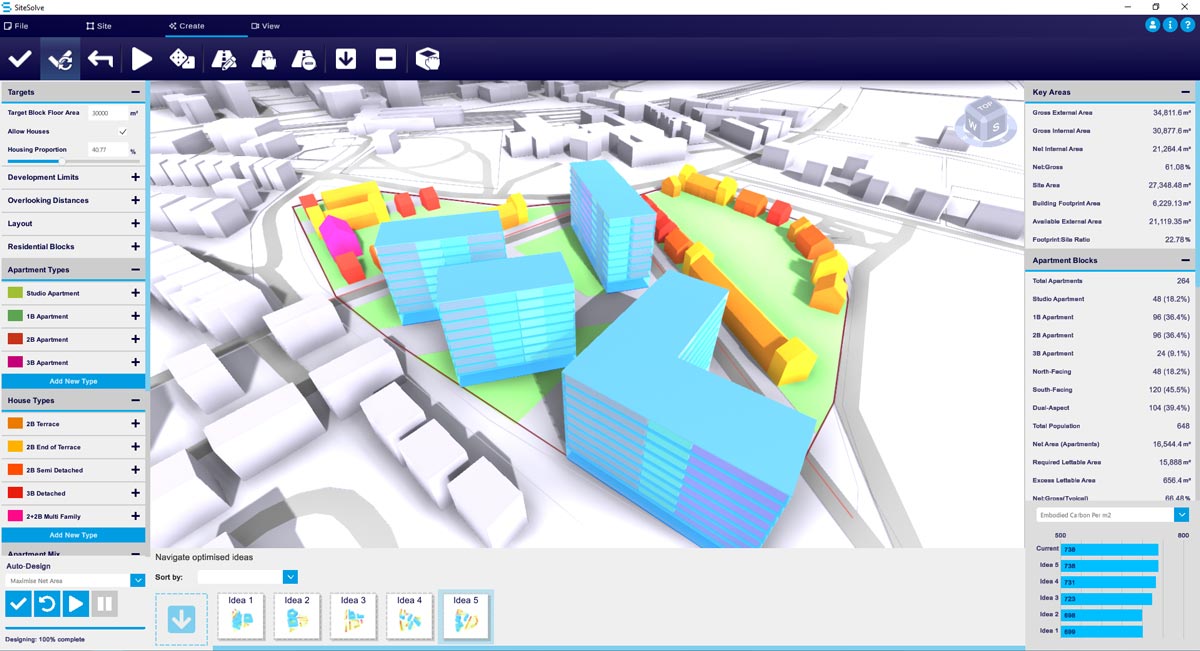
Transport for London (TfL) needed 2,200 separate sites with a combined area of over 16 million m2 assessed for development potential. Ramboll used an in-house tool to explore site geometry, access, site-specific constraints, and preferences to generate potential site developments automatically and hence estimate likely cost, value, and return on each site.
This approach allowed greater quality of information early in the project and to achieve scheme design assessment at scales that are impossible without automation.
Smakkelaarspark
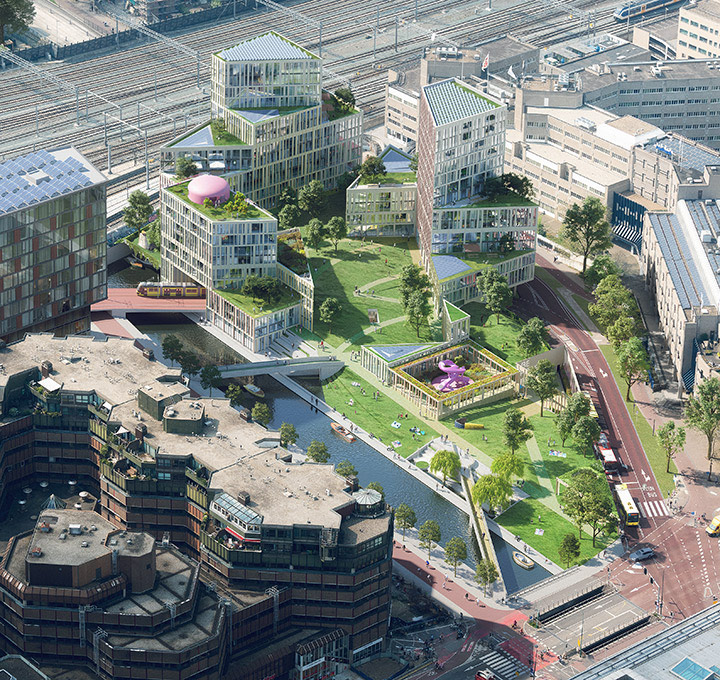
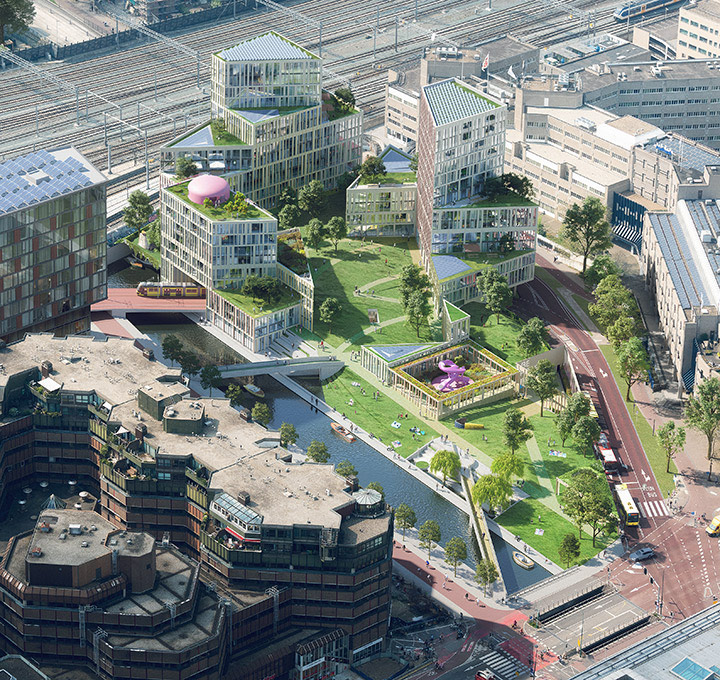
Arup, Lingotto, Studioninedots, and ZUS used Computational Design to deliver the competition-winning proposal for the new residential development in Smakkelaarsveld, Utrecht. The site is heavily congested, surrounded by major roads, a railway, and a station, and crossed by bus and tram lines, waterways, overhead cabling, and underground services.
The team used generative modelling methods to explore the 1012 possible design options and find a design that maximised park area and light while providing 20,000 m2 of residential properties and satisfying the site constraints.
Elements
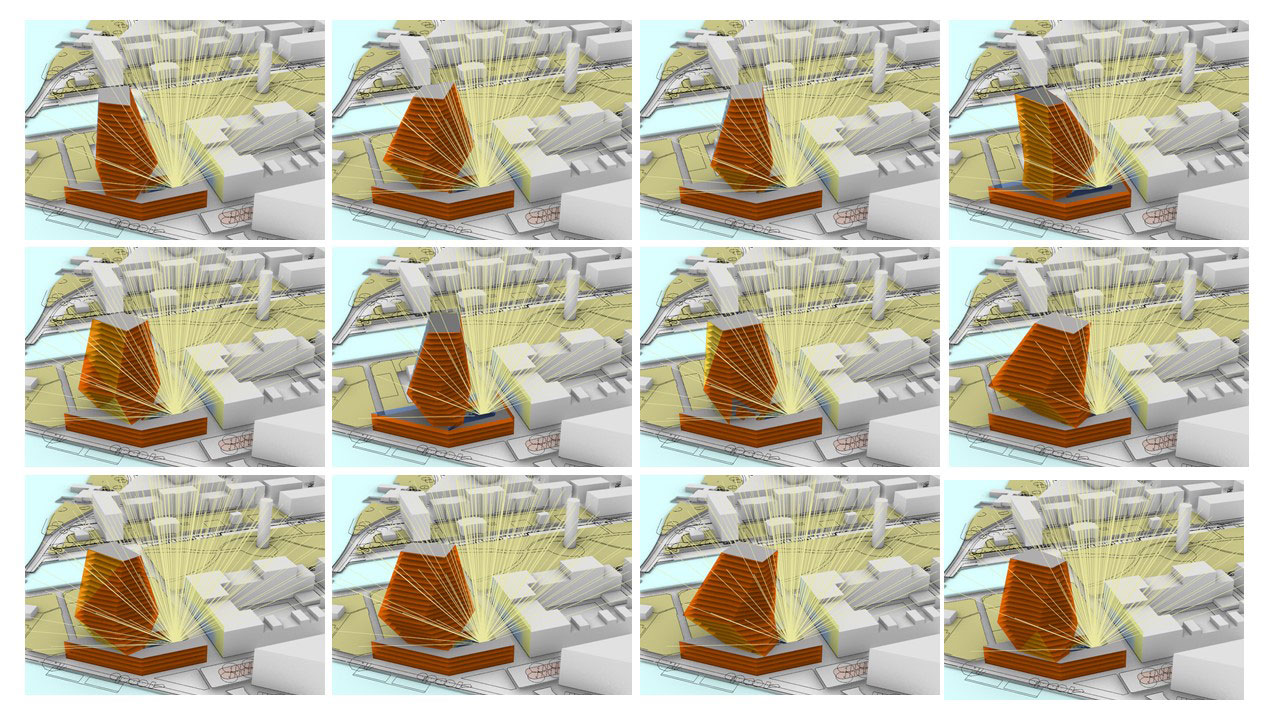
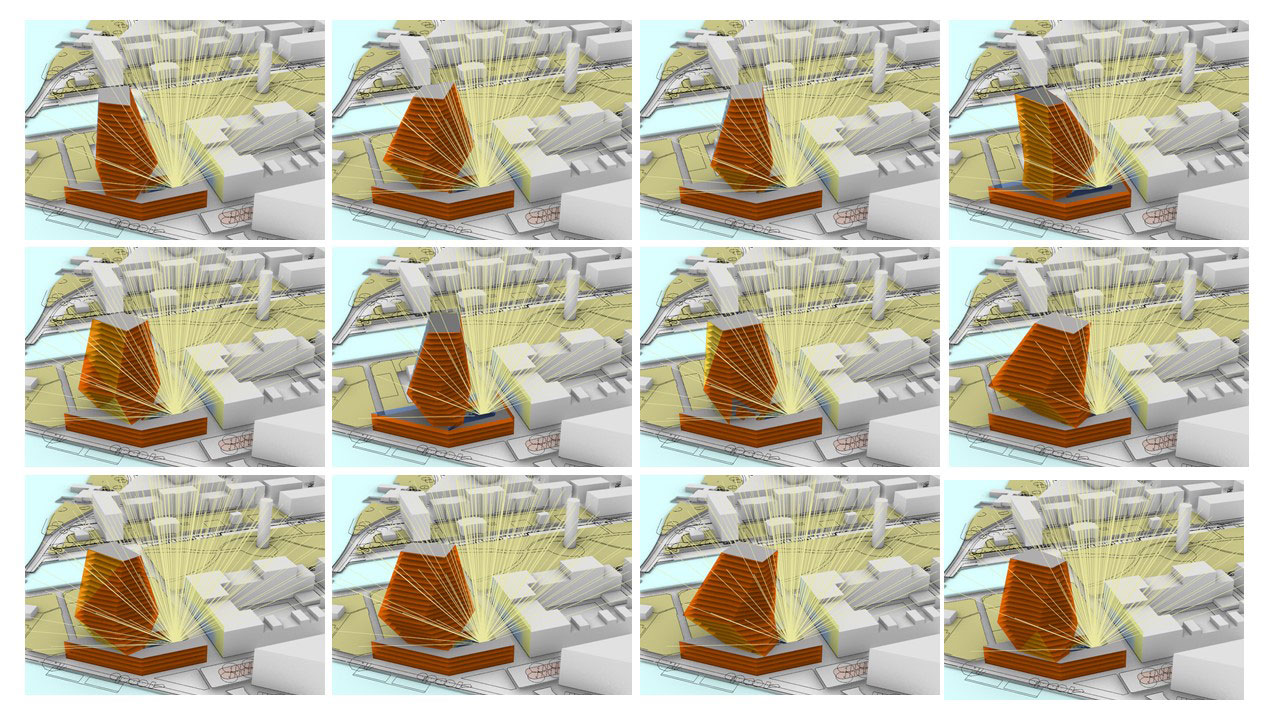
Elements is a new 70 m tall hybrid timber | steel | concrete residential building in Amsterdam by Arup, Kondor Wessels Vastgoed, Koschuch Architects, and Boom Landscape and Buildung. The design requirement was to optimise daylight, water collection, wind, and fresh air, green spaces, energy generation, 114 residential properties, commercial facilities, and a green roof garden.
Genetic algorithms were used to generate hundreds of design variants, which were automatically assessed against the design criteria; the best were then fed back into the system to develop the next generation of improved designs.
Aarhus Botanical Garden Tropical Hot House
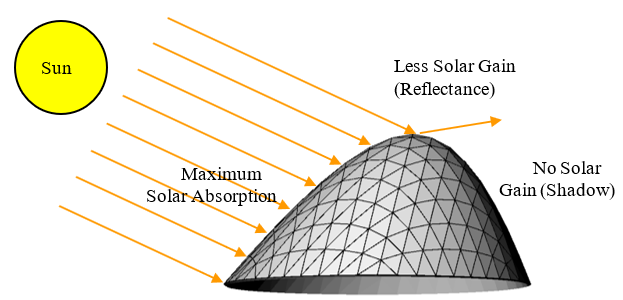
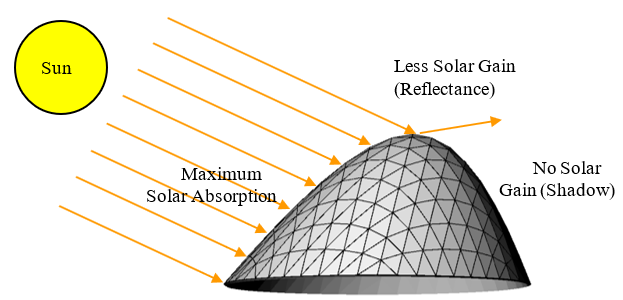
The University of Aarhus’s competition to design a new tropical hothouse was won by the team of C.F. Møller Architects, Søren Jensen Consulting Engineers, and Paul Shepherd of Bath University. They used a combination of parametric design and integrated optimisation to find the hothouse geometry that maximised solar gain in the winter and minimising it in summer, thus minimising the requirement for both winter heating and summer cooling—all in a domed, glazed structure large enough to house the tall tropical trees.
The result won both the commission and the Chicago Athenaeum award for International Architecture, plus many other commendations.
Camp Adventure Forest Tower
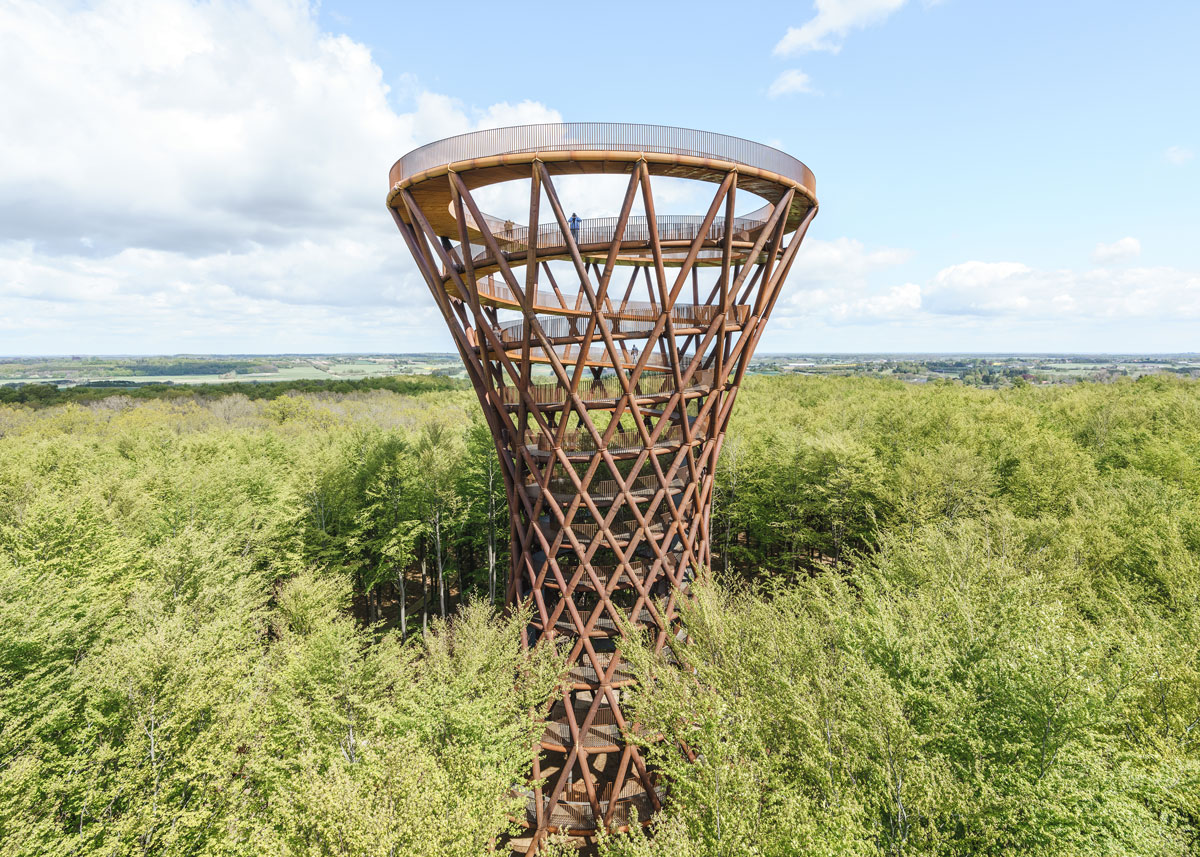
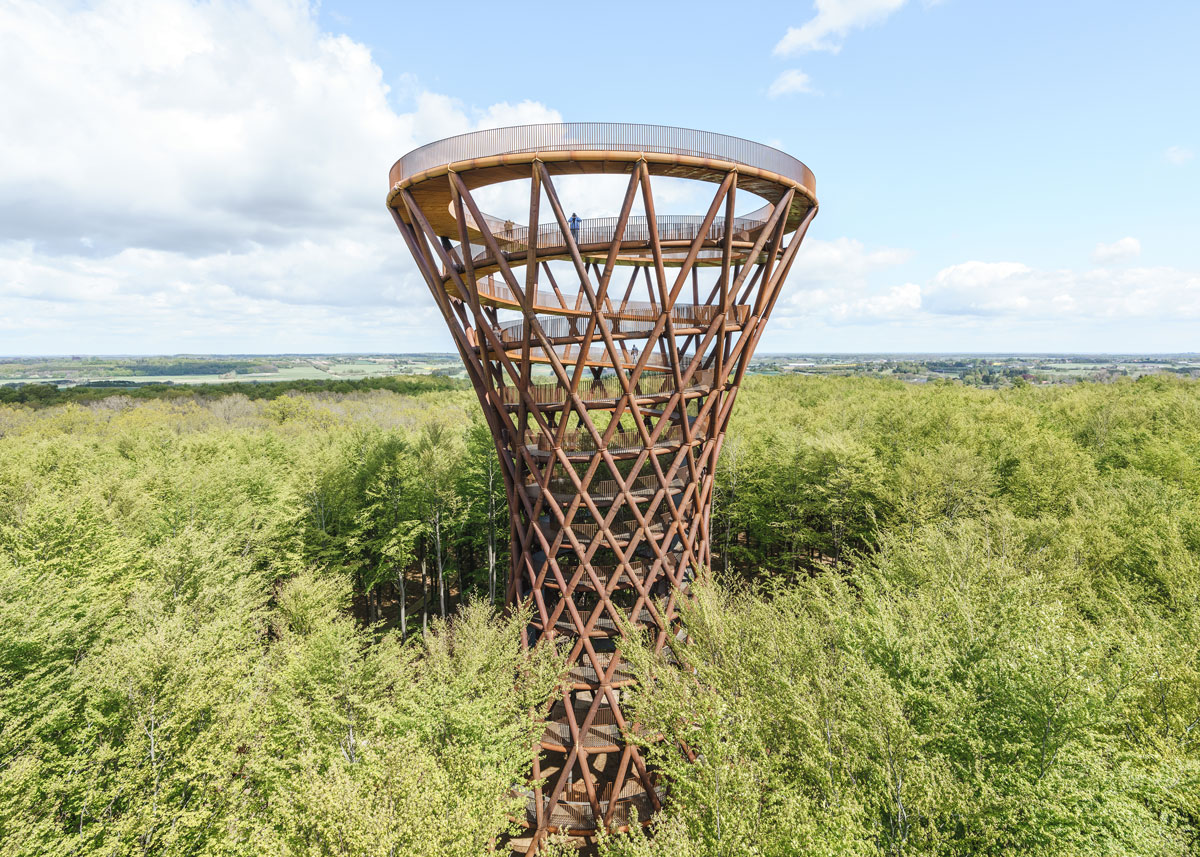
This project resides deep in the Danish countryside. Following a kilometre-long walk through the forest, a ramp rises 45 m through the canopy into the sunlight above, suspended by an elegant hyperboloid tower.
The Camp Adventure tower, designed by EFFEKT and engineered by Arup, is a double-ruled surface, which means that its doubly curved form is comprised entirely of straight elements, steel columns in this instance. Arup rapidly analysed and assessed the form options within Rhino/Grasshopper to find the one most resistant to buckling before exporting to GSA for detailed analysis and to CAD programs for coordination and documentation. The result was crowned one of TIME Magazine’s World Greatest Places and won international architectural and tourism prizes.
Ken Rosewall Arena
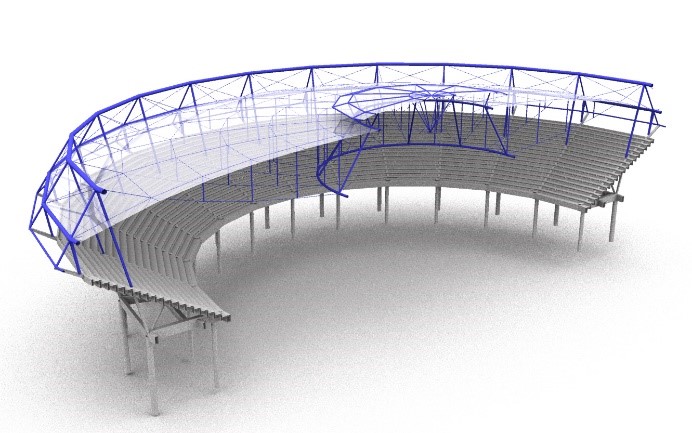
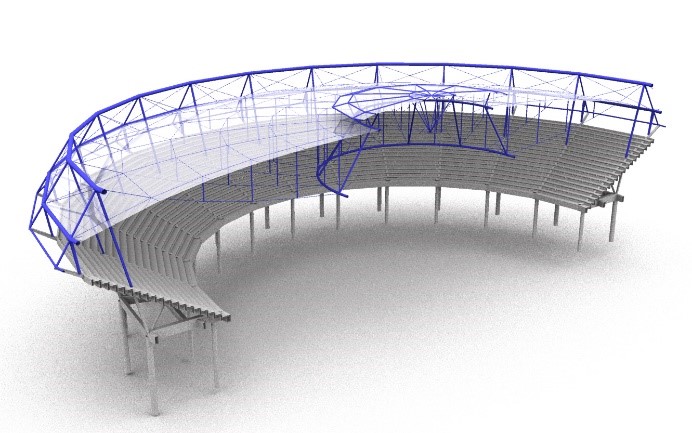
In the Sydney 2000 Olympics, the Ken Rosewall Arena wowed the tennis world and won architectural awards. Over 20 years later, Arup were called in again, accompanied by Cox Architecture and Fabritecture, to upgrade the arena and transform it into an all-weather covered venue.
The 100 m diameter area was built on a brownfield site with contaminated soil, which meant that while the new roof had to cover a significantly larger area, it could not increase the loads on the foundations. The solution was to exchange the cantilever canopies with Australia’s first major radial cable net roof.
Advanced form finding and intelligent design, combined with a complete digital workflow and documentation, meant that the layout, details, and connections were all delivered to the project partners and procurement chain via 3D files rather than 2D drawings. This enabled the team to greatly extend the roof without increasing the loads and within a tight timetable.
Conclusion
The above projects all showcase different aspects of Computational Design, achieving results that would be extremely difficult using traditional methods and almost certainly not to the same levels of quality and efficiency. This is the design methodology that the building industry needs to meet current and future demands for low-carbon construction.
About the author


View the original article and our Inspiration here
Leave a Reply