The shipbuilding world may seem far removed from the construction industry, but valuable lessons can be learned from how ships are assembled using modular and lean methods.
Minna Rosvall of YLE wrote an article about how cabins are manufactured using Takt production at the Piikkiö Works factory in southwestern Finland. The factory has operated for 40 years and is now part of the Meyer Group, whose Turku shipyard is its primary customer.
Takt production
Rosvall describes how cabin modules move smoothly down the assembly line in the spacious hall at a leisurely yet consistent speed. Cabins are produced from the line every 15 minutes, totaling 120 weekly units.
The process reminds that of car assembly. CEO Ari Kumpulainen explains the workflow, stating that as one worker finishes their task, the cabin moves to the next worker’s station. The next set of workers enters the cabin to perform their functions.
In an interview for the Aboard magazine, Production Manager Lauri Laakso said: “The assembly of a module starts by attaching the first wall element to the bathroom floor. That is followed by over 40 different work stages before the final inspection.”
Sturdy plastic-wrapped cabin packages are neatly organized on shelves in the storage area, with enough space to accommodate 500 modules simultaneously.
The completed cabins are transported to Meyer’s shipyard. One shipment contains three cabins, each from 15 to 25 square meters in floor area.
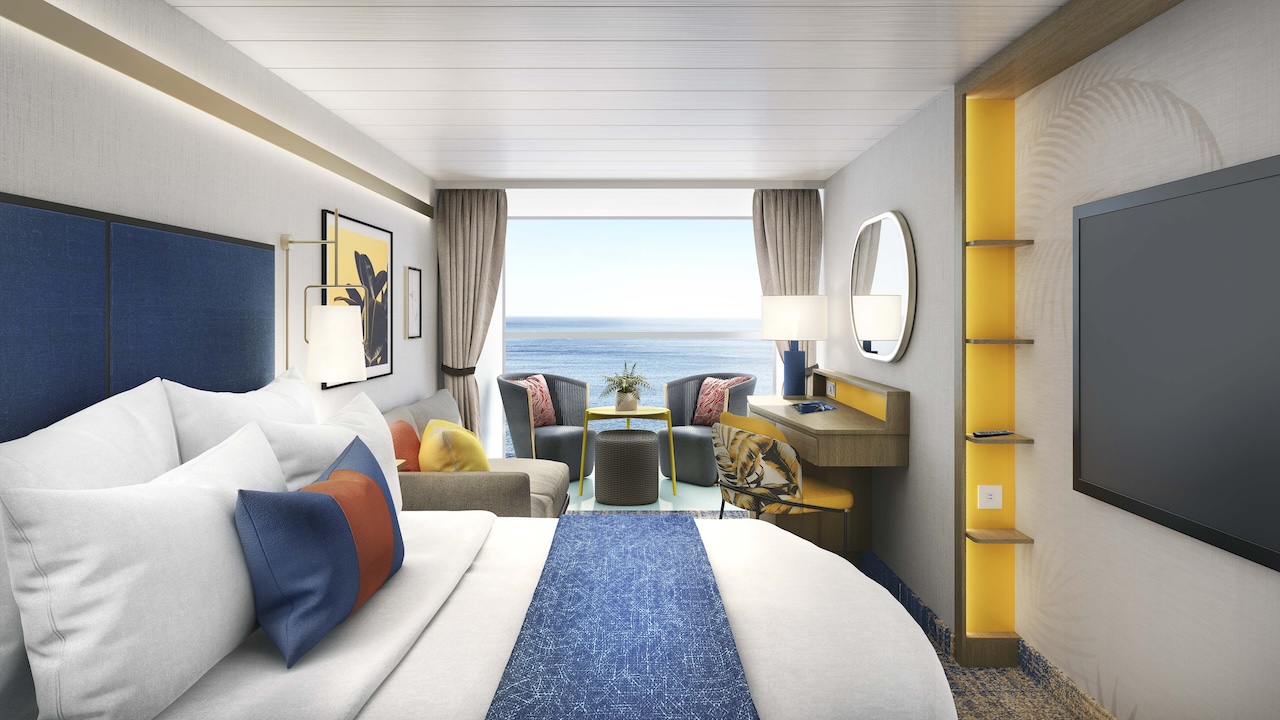
Products for the biggest cruisers in the world
Piikkiö Works provided the cabins for the largest cruise ship in the world, the Icon of the Seas for Royal Caribbean International. At Meyer’s Turku shipyard, cabins are already being installed for its successor, the Star of the Seas, which will be completed in the summer of 2025.
One large cruiser contains around 4000 cabins. Cabins may look similar but vary in dimensions and electrical and plumbing installations. Clients occasionally request changes to small details, such as the placement of toilet paper holders or toilet brushes.
Other modular products
During peak times, the plant employs up to 300 workers. The Icon-class cruisers cover 80 percent of the factory’s production, but there can be quieter periods in shipbuilding. During those times, Piikkiö Works can build cabins for other clients, VR, the local train operator, being one of them.
According to Aboard, the company has previously also manufactured room modules, for example, for the Children’s Hospital in Helsinki and the Torni Hotel in Tampere.
The takeaway
The Meyer Group and their Piikkiö Works factory demonstrate the efficiency of industrialized production of complicated and customized products. The question arises: what would it take to achieve the same level of industrialization in construction?
The images are courtesy of Royal Caribbean International
View the original article and our Inspiration here
Leave a Reply