The Royal Institution of Chartered Surveyors (RICS) regularly publishes interesting reports about construction worldwide. I found their latest construction productivity report interesting. Two things stuck out for me: how companies measure productivity and what productivity interventions are most impactful.
The report was based on RICS’ Q3/2023 Global Construction Monitor data, which surveyed 3285 company responses.
How companies measure labor productivity
There is no universal way to report construction labor productivity, making comparing results in various countries, areas, and companies difficult.
The RICS survey suggested seven alternatives to choose from:
- Output per worker hour
- Productive worker time per total worker time
- Value of work completed per worker hours
- Value of work completed per worker costs
- Earned value over the actual cost
- Earned hours over the actual hours
- Worker hours per functional unit of the asset
The most preferred definition of labor productivity globally is ‘earned value over the actual cost,’ accounting for 26.8% of all respondents. However, ‘output per worker hour’ was used most in the Americas. The least popular in all regions was ‘worker hours per functional unit of the asset.’
Construction equipment and tools matter least for productivity
In one section of the survey, respondents were asked to rate the impact of different factors on labor productivity. The global results are shown in the following chart.
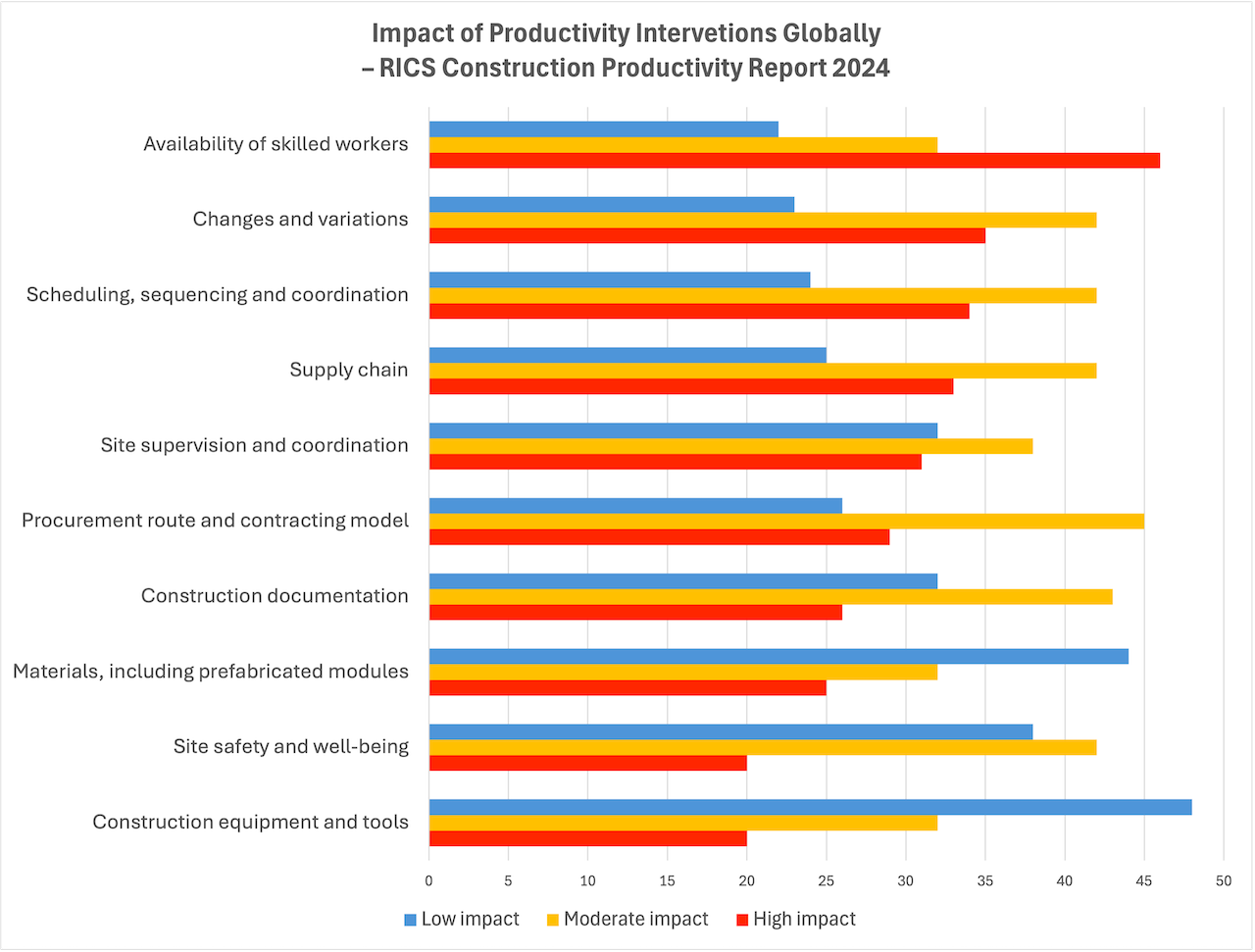
The availability of skilled workers ranks the highest regarding its impact on productivity, with 46% of respondents confirming its importance globally. Only 25% think that materials, including prefabricated modules, have a high impact.
Construction equipment and tools were deemed to have the most negligible impact. 48% said they have a low impact on productivity. This result indicates that technologies per se do not matter, but how they support other productivity interventions is crucial.
These results are opinion-based but resonate with some other studies. Still, it would be great to have some factual data on these aspects of productivity.
A Finnish perspective
Finnish magazine Rakennuslehti reported in their latest issue about how the Confederation of Finnish Construction Industries RT wants to measure productivity in the construction value chain. They suggest ‘hours per square meter’ as the standard. That metric would consider the productivity of the whole supply chain, not just the site.
Staffan Fagerudd used this metric in his master’s thesis, supervised by Professor Antti Peltokorpi from Aalto University and Antti Aaltonen, Construction Development Director at RT.
Fagerudd determined the hours required to complete one gross square meter of a precast concrete apartment building in Finland. On average, 13 hours were needed, of which one hour was spent on design, two hours on prefabrication, and 10 hours on on-site construction work. The manufacturing of building materials and earthworks were not included in the figure.
The magazine article contains an interesting tidbit based on the data that Singapore’s Building and Construction Authority collects. When comparing privately funded apartment buildings, Finnish sites complete twice as many square meters in a workday than their Singaporean counterparts.
Measure consistently to improve
The common claim that the construction industry’s productivity has flatlined may be valid using some metrics but is not the overall truth. Typical statistics don’t include, for example, the apparent productivity increase in prefabrication plants.
Today’s technology allows us to measure productivity during all project phases. Establishing meaningful and impactful standards to measure productivity would help improve it.
View the original article and our Inspiration here
Leave a Reply