In a recent conversation with three experts from the China Construction Third Engineering Bureau, Mr. Pei Yijun, Dr. Yang Hui, and Ms. Liu Jiao, I had the opportunity to explore two breakthrough innovations that are reshaping high-rise construction and building services integration in China.
The two technologies we discussed were the Intelligent Micro Bump Jacking Formwork System and the Design-Prefabricate-Transport-Assemble (DPTA) model. These technologies reduce build times, improve safety, and point toward a more digital, modular future for construction worldwide.
The three experts from the China Construction Third Engineering Bureau (CSCEC 3rd Bureau) each have distinguished careers marked by deep technical expertise and a commitment to advancing construction innovation.
Mr. Pei Yijun is the Chief Engineer of the Bureau’s installation engineering subsidiary and a nationally certified First-Class Constructor with nearly 30 years of industry experience. Dr. Yang Hui, a senior engineer and deputy director at the China Academy of Advanced Construction Technology, brings over a decade of R&D expertise in high-rise construction systems. Ms. Liu Jiao, Chief Engineer for the Northwest Region of the Bureau’s digital division and a former student of Mr. Pei, has led the development and implementation of DPTA.
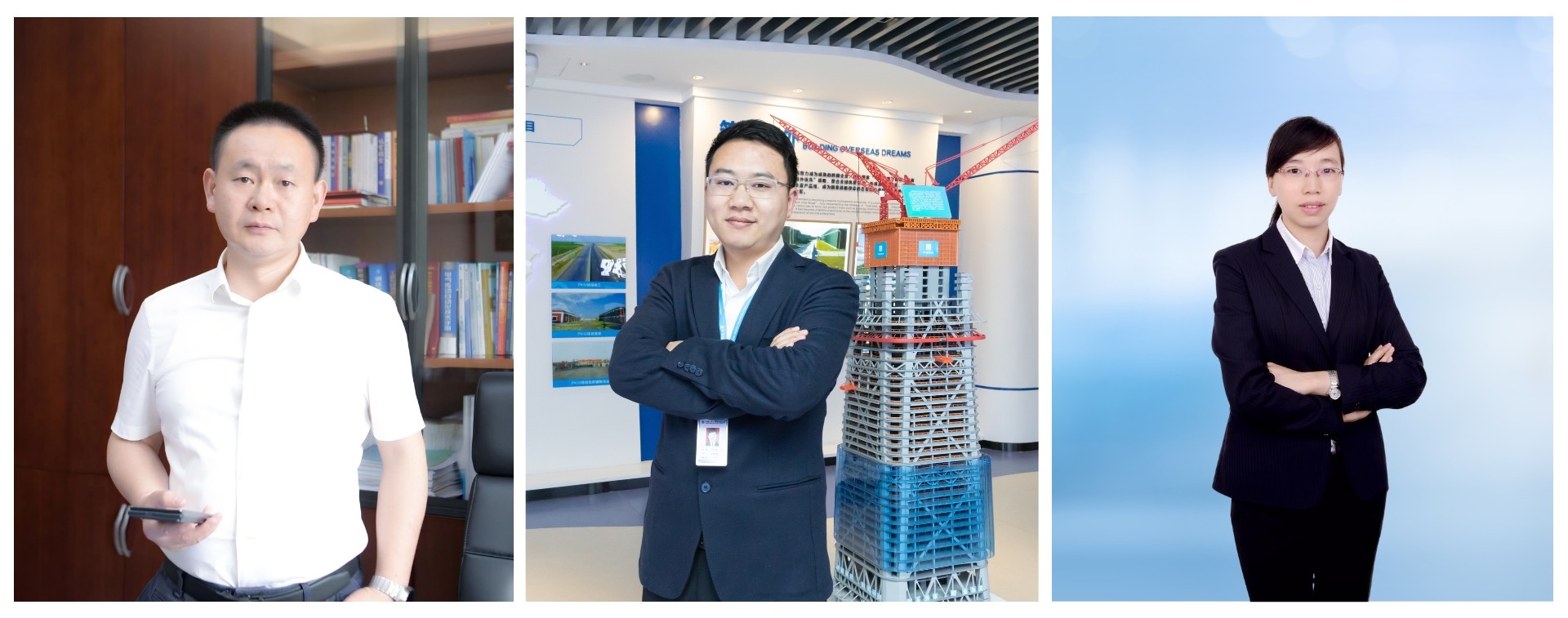
A Factory in the Sky
The Intelligent Micro Bump Jacking Formwork System, colloquially called a “building machine,” was born out of necessity in 2007. At the time, China’s skyline was rapidly reaching new heights, with projects often exceeding 400 meters. Traditional formwork systems were becoming inefficient and unsafe for such extreme conditions. Drawing inspiration from industrial factories, the team envisioned a modular, self-jacking platform that could create a safer, more integrated construction environment at altitude.
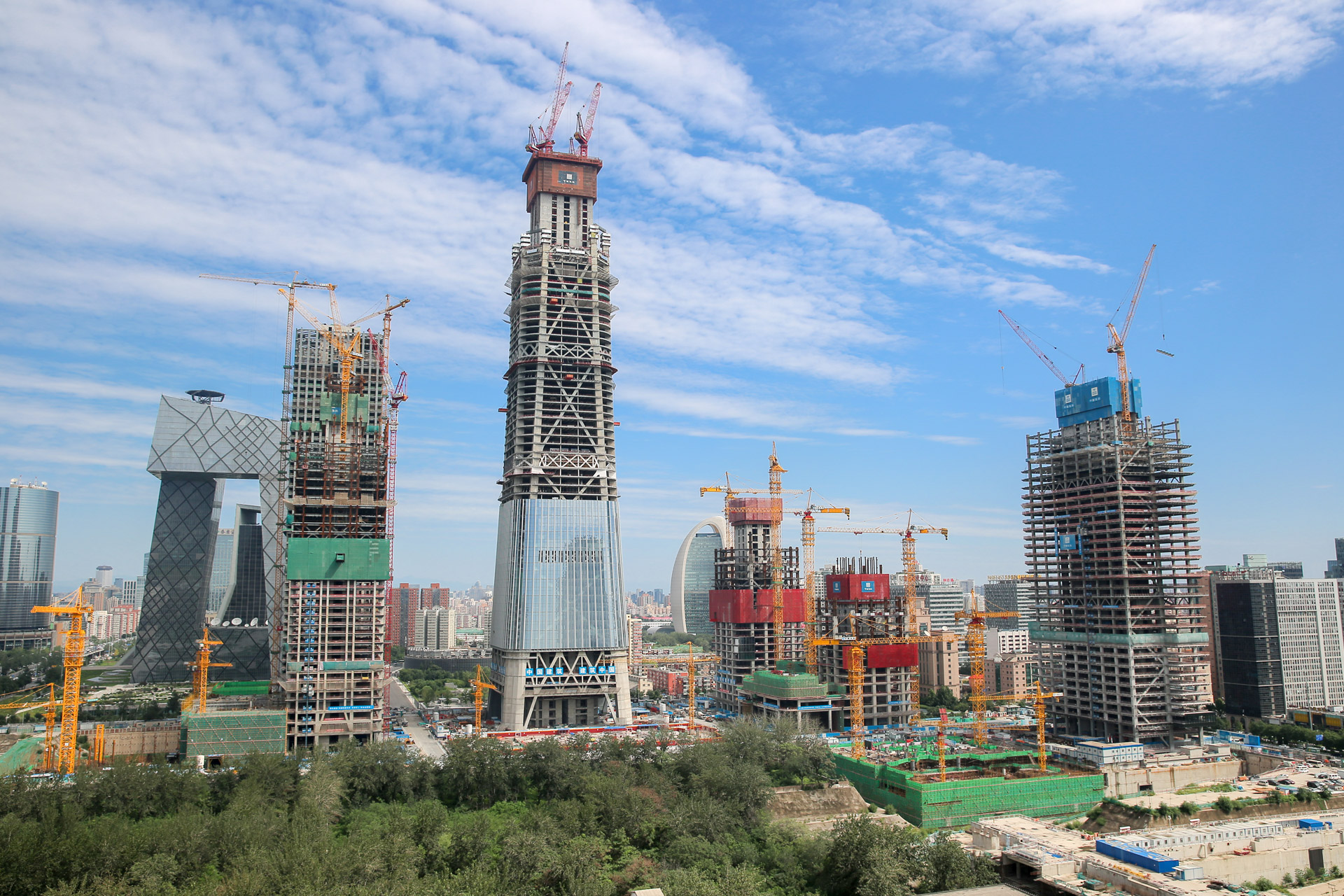
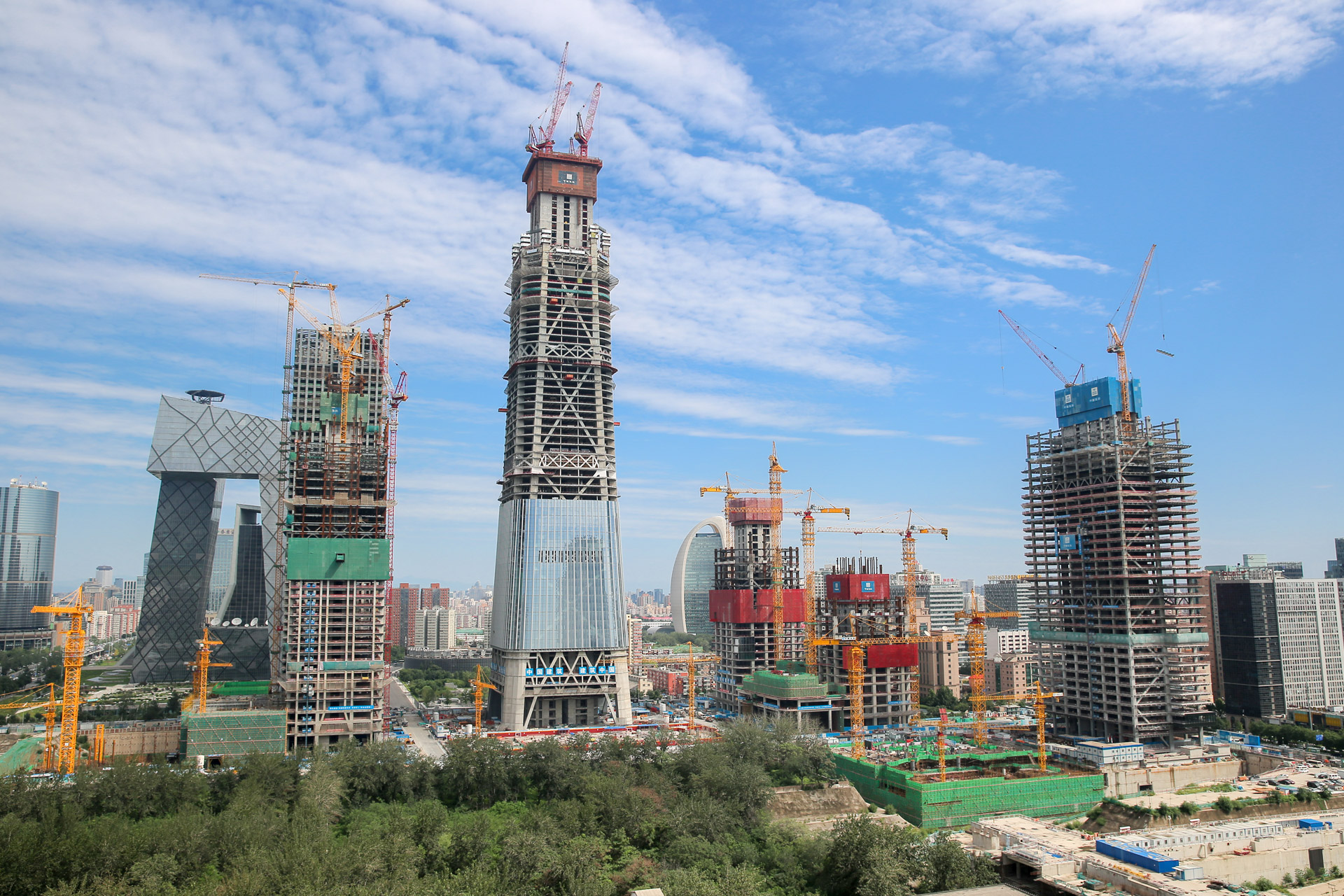
Unlike conventional climbing formwork or slip form systems, this platform is essentially a high-altitude, multi-story factory. It incorporates not just structural formwork, but also cranes, concrete distributors, and worker areas; all protected in a sealed, wind-resistant enclosure. The design allows multiple trades to work simultaneously in a controlled environment, even hundreds of meters above ground.
The platform’s carrying capacity is particularly noteworthy. On the China ZUN Tower in Beijing, a 528-meter-tall skyscraper with 118 floors, the system supported four tower cranes and dramatically accelerated the construction timeline. Shaving one day off the average five-day-per-floor schedule saved over 100 days on the total construction period. According to Dr. Yang, this efficiency translated into a total cost saving of around 60 million RMB (over 8 million USD), including direct and indirect expenses.
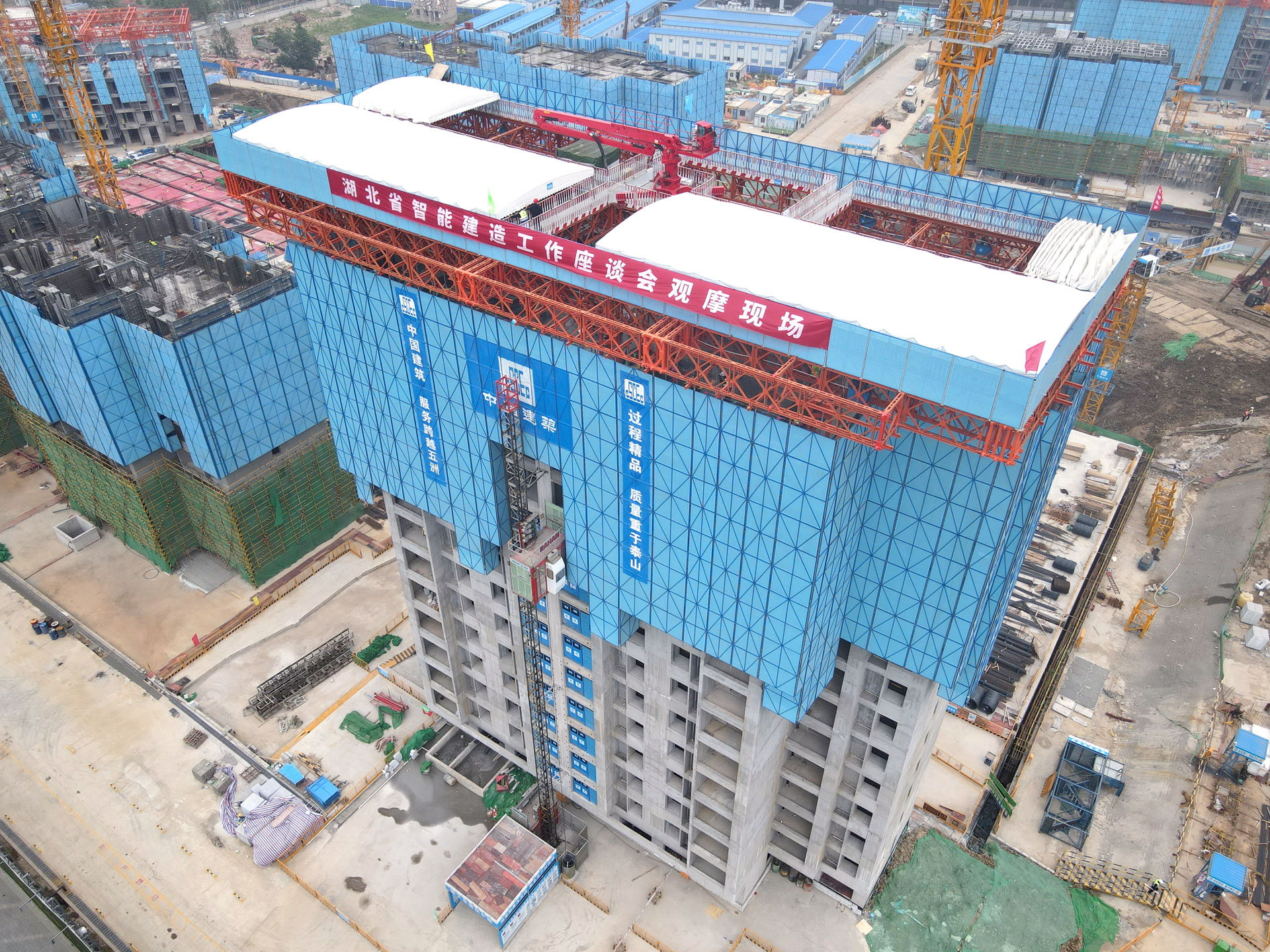
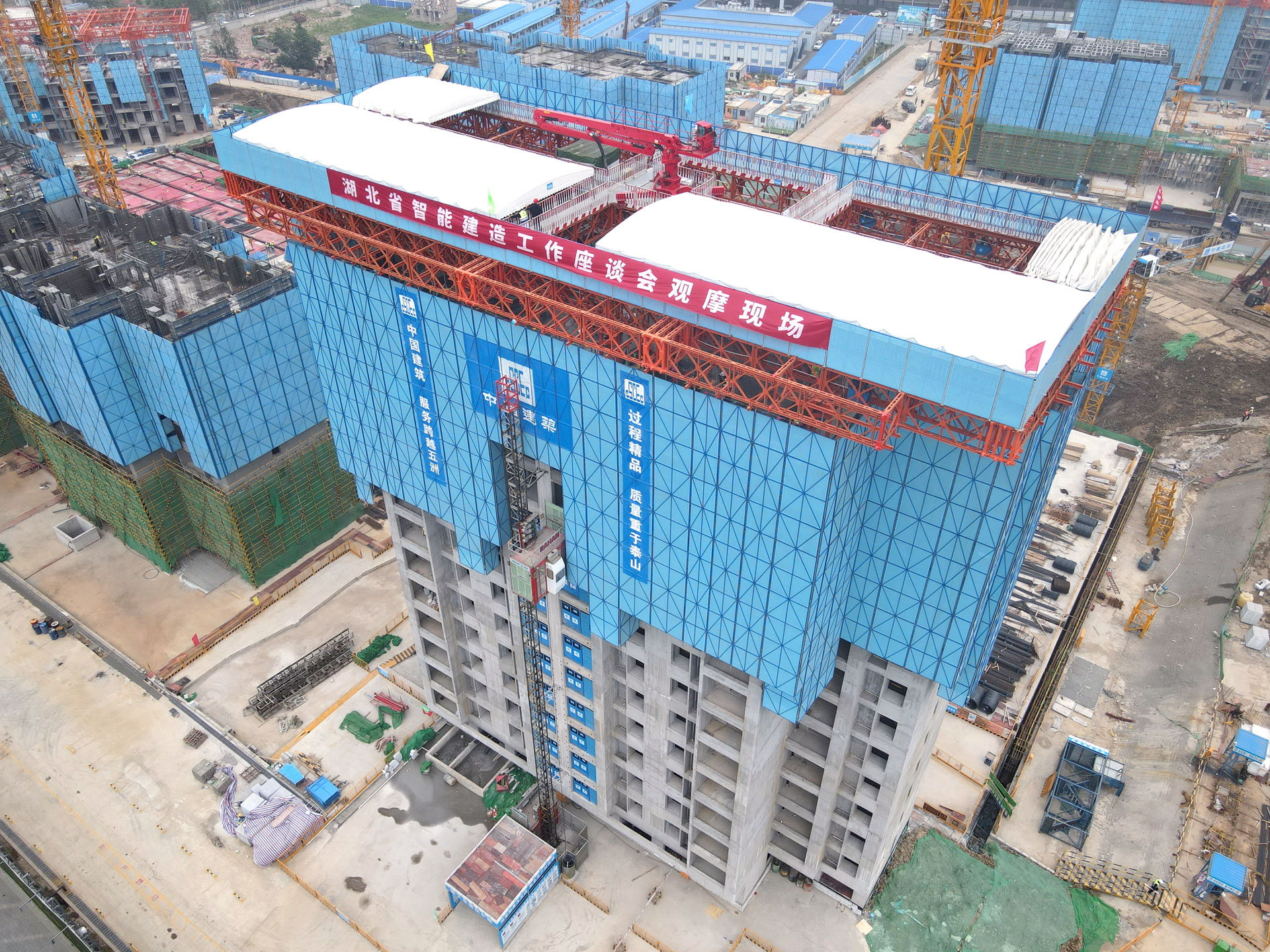
Challenges and Ambitions
Despite its success, implementing the system was not without difficulties. High tolerances are required during both off-site fabrication and on-site assembly. Structural discrepancies, installation errors, and mechanical damage during daily use remain concerns. Additionally, skilled labor and cross-disciplinary engineering expertise, including mechanical, hydraulic, electrical, and structural, are essential for deployment.
Looking ahead, Dr. Yang sees the building machine evolving into something akin to a “lightless factory”, an automated, sensor-driven platform with minimal human intervention. The vision includes robotic systems, IoT-based remote monitoring, and digital integration, enabling real-time decision-making and predictive maintenance.
Through continuous research and development iterations, the team has expanded the application scenarios of building machines from constructing skyscrapers to ordinary residential buildings, bridges, nuclear power engineering, and other fields.
While there is growing interest abroad, including in the Middle East, adaptation to international markets has been relatively slow. The system requires a robust steel fabrication supply chain, something not always available outside of China. However, the team remains optimistic about the technology’s global potential, especially as demand grows for safer, faster, and more sustainable construction methods.
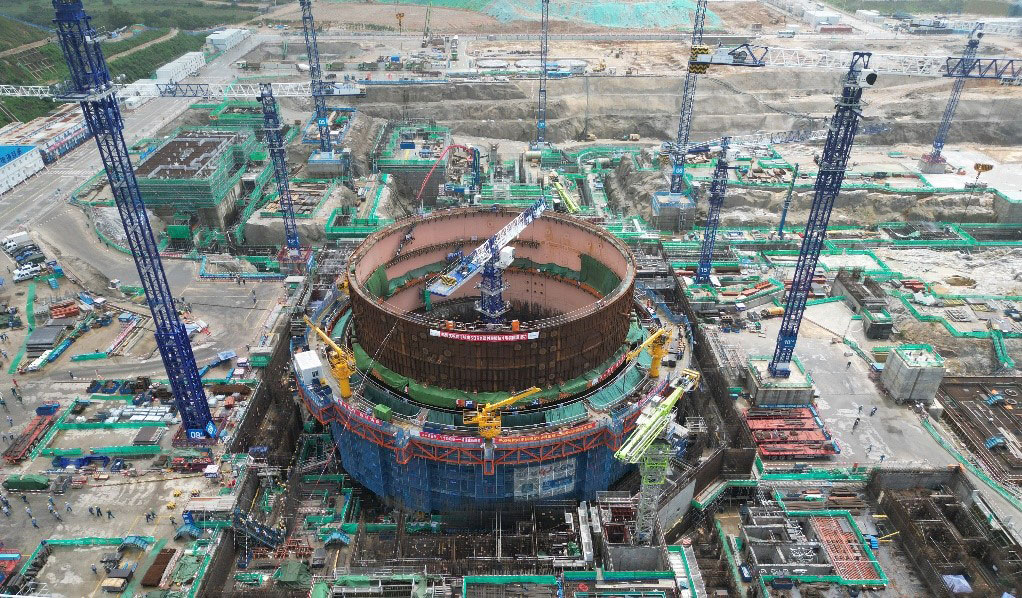
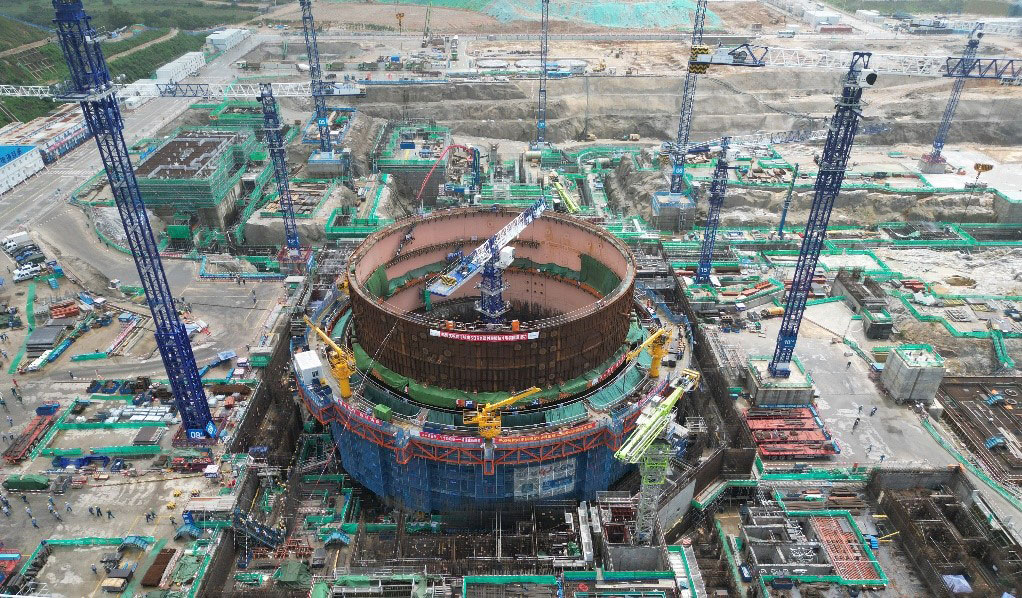
DPTA: A Modular Revolution in MEP
Where the jacking formwork system revolutionizes vertical construction, the DPTA model brings modular efficiency to MEP (Mechanical, Electrical, Plumbing) installations. Conceived and championed by Ms. Liu, DPTA stands for Design, Prefabricate, Transport, and Assemble. It focuses particularly on complex areas like pump rooms, which often become bottlenecks in high-rise and infrastructure projects.
DPTA modules are pre-designed using BIM tools like Revit, MagiCAD, and Solibri. The design team also considers the product’s logistics, such as optimizing the transport to the site.
The design is translated into detailed shop drawings and then fabricated in nearby factories. Modules weighing up to 8 tons and measuring roughly 2.5 meters long are transported to the site, where they are lifted into position by crane and assembled with minimal on-site work. Ms. Liu noted that the assembly is like putting Lego blocks together.
One early pilot project in Xi’an used 11 modules in a 200-meter-tall building. Since then, the CSCEC 3rd Bureau has implemented DPTA in more than 200 projects across China, and the team has secured over 60 patents. Use cases range from office buildings and stadiums to subway systems, where standardization is exceptionally high.
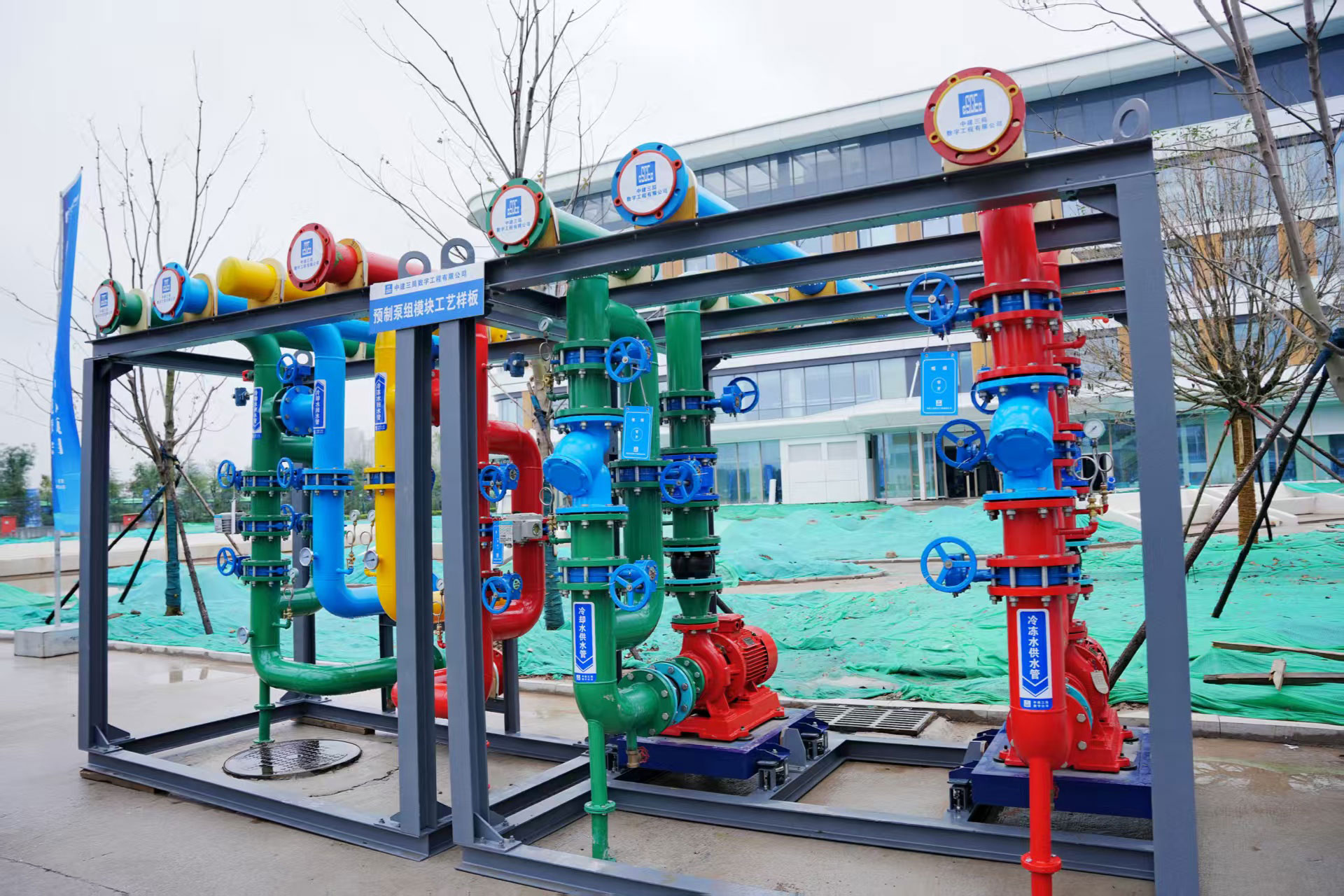
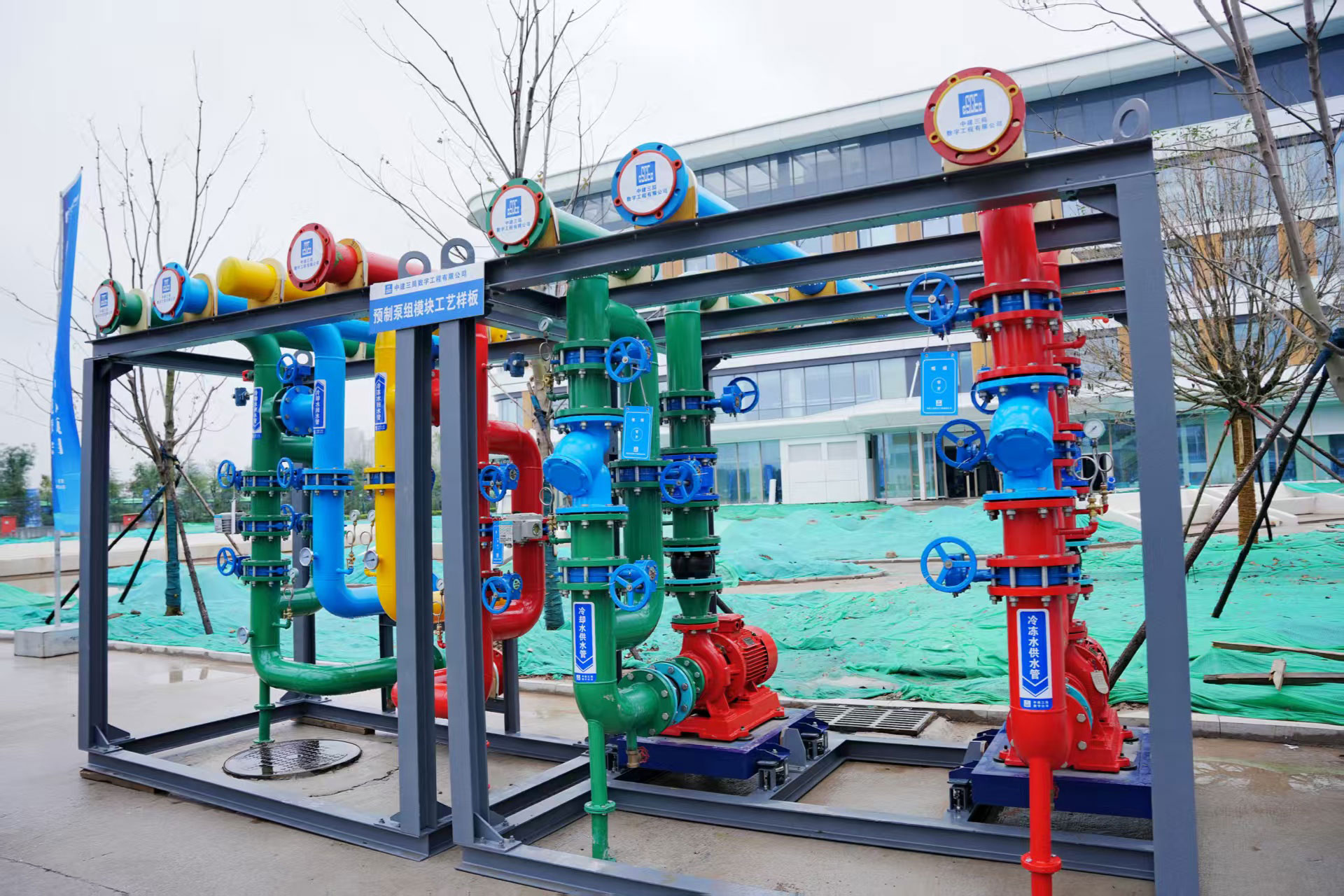
The Fivefold Advantage
DPTA’s advantages are significant and measurable:
- Time Savings – By shifting MEP work from site to factory, projects avoid scheduling conflicts and delays due to environmental conditions.
- Higher Quality – Precision manufacturing in controlled settings results in fewer errors and virtually eliminates rework.
- Cost Efficiency – Labor costs are reduced and material waste minimized. The digital fabrication process is both accurate and scalable.
- Ease of Implementation – Local factories can produce the modules without requiring high-end proprietary equipment.
- Sustainability – Factory-based work reduces noise, dust, and emissions at the construction site, creating a cleaner and safer environment.
Yet, as with any innovation, DPTA has faced challenges. Early on, mismatches between as-designed and as-built dimensions, whether from fabrication inaccuracies, site conditions, or worker errors, led to misaligned modules. To counter this, the team introduced feedback loops, remeasuring built structures before fabrication, and investing in more accurate manufacturing equipment. They’ve also created a trained workforce of specialized construction workers, many of whom participate in both fabrication and installation.
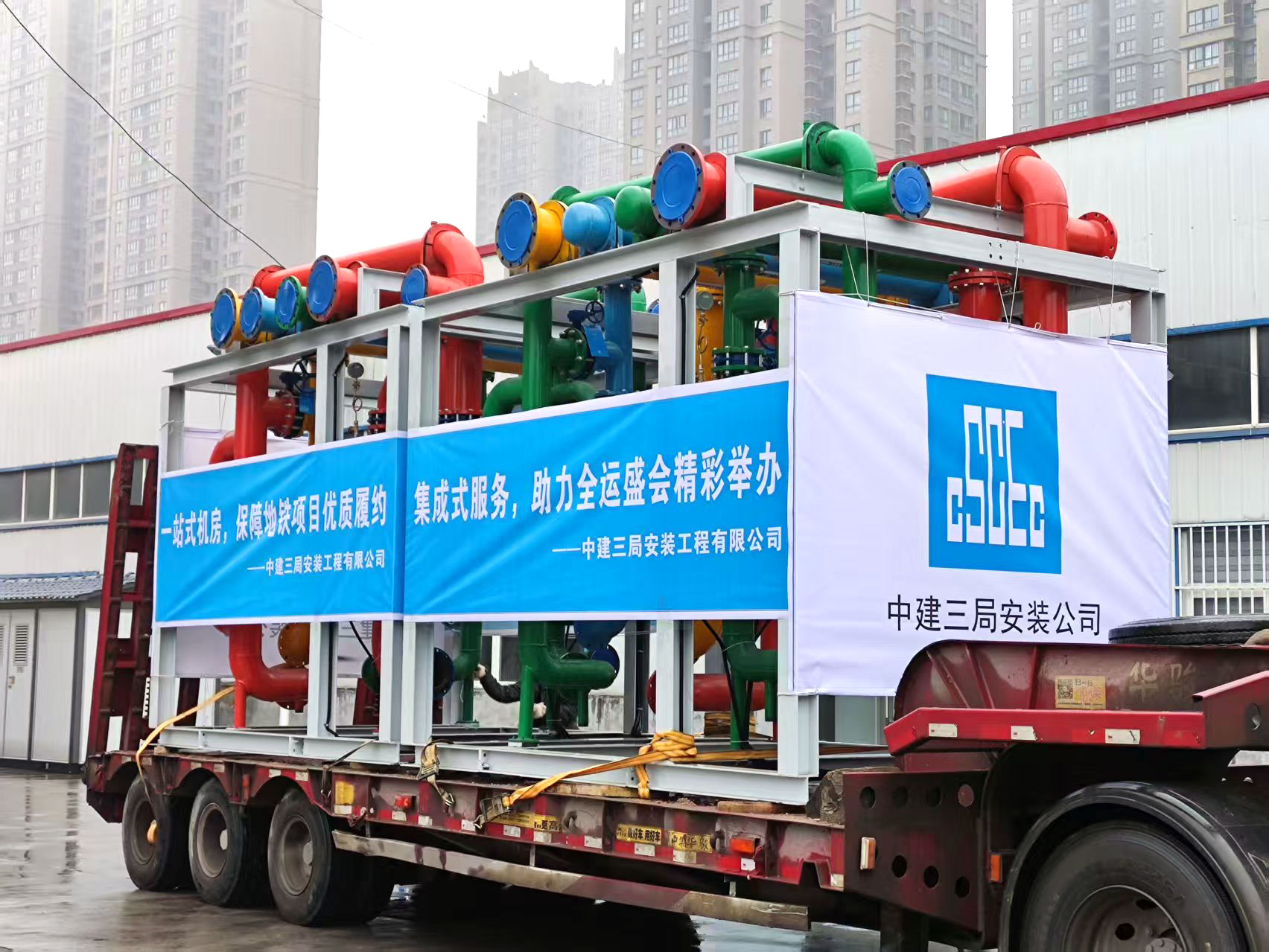
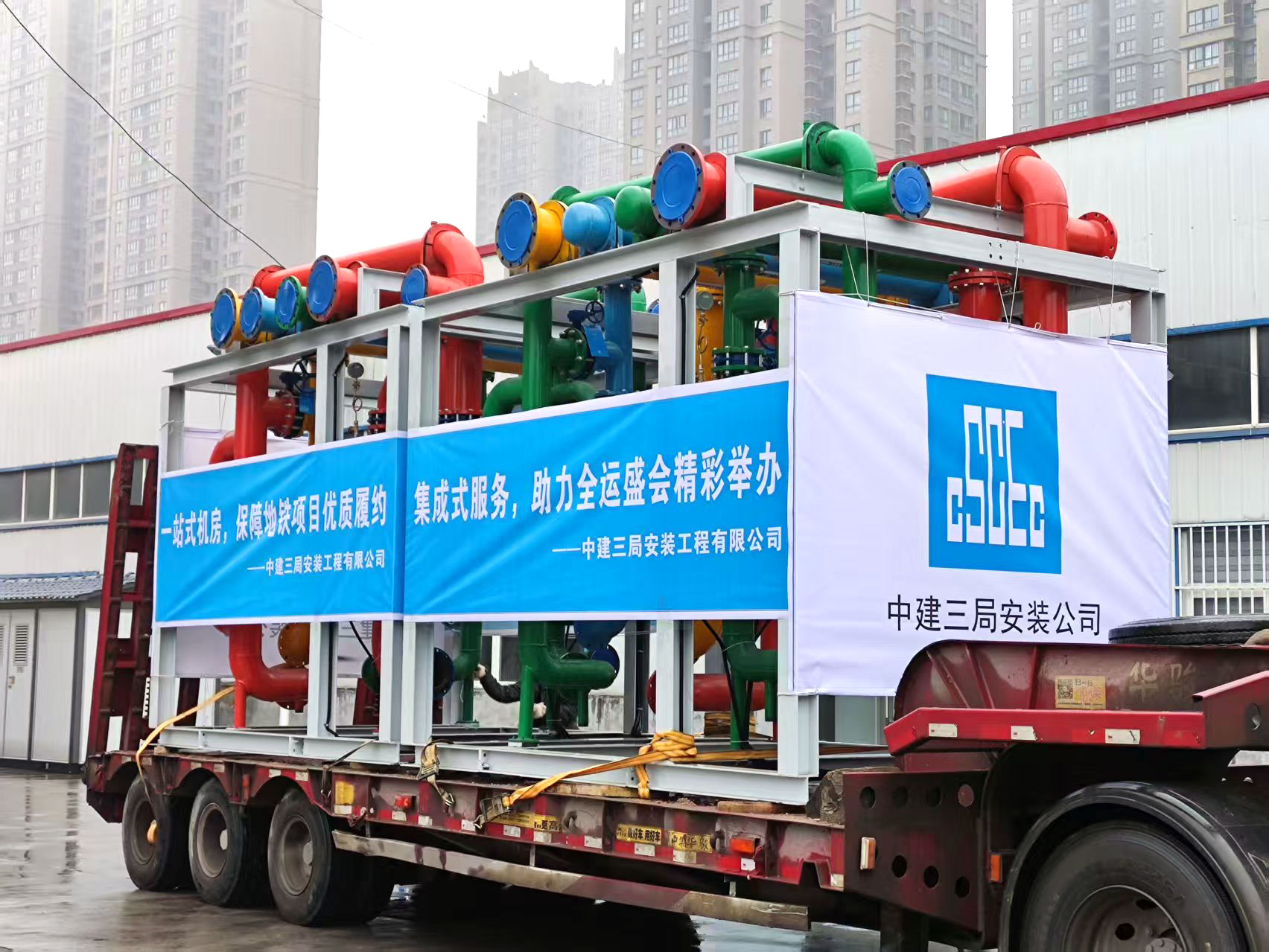
A Template for Global Transformation?
Both the formwork platform and DPTA model exemplify a shift in construction thinking: from site-based improvisation to factory-style predictability. As Mr. Pei noted, their firm’s integrated approach to handling design, construction, and operations under one umbrella has been crucial for success.
While these innovations were developed for the unique demands of China’s urban boom, they offer valuable insights for international markets seeking to improve construction efficiency, safety, and sustainability. With further development, localization, and strategic partnerships, these technologies could help solve global housing, infrastructure, and other challenges.
The images are courtesy of the China Construction Third Engineering Bureau. The title photo is the 474-meter-high Greenland Center in Wuhan.
Special thanks to Mr. You Yang, Product Operations Director at Glodon, for organizing and facilitating the discussion with the experts.
View the original article and our Inspiration here
Leave a Reply