Chinese construction has been in the headlines for record-breaking speed: a 10-story residential building erected in 28 hours and 45 minutes, or a 57-story skyscraper built in 19 working days. These projects rely on meticulous planning, extreme prefabrication, and clockwork execution.
Besides those unique showcase projects, I wanted to learn how Chinese AEC firms are industrializing construction at scale. My recent conversation with three China Construction Third Engineering Bureau (CSCEC 3rd Bureau) experts shed light on two breakthrough technologies that exemplify this shift.
Two strategies for industrialization
As the construction industry evolves, two powerful strategies are emerging to drive industrialization: bringing construction into the factory or bringing the factory to the construction site.
In China, both approaches are being deployed at scale, underpinned by digitalization, particularly the use of BIM.
The factory in the sky
The Intelligent Micro Bump Jacking Formwork System, or “building machine,” represents the strategy of bringing the factory to the jobsite.
This multi-story, self-climbing platform transforms each level of a high-rise into a weather-resistant, enclosed production environment. It integrates cranes, concrete distribution, and workspaces, enabling multiple trades to operate simultaneously, safely, and efficiently, even at heights of over 500 meters.
Used on landmark projects like the China ZUN Tower in Beijing, the system reduced the construction schedule by over 100 days and saved millions in costs.
The next-generation vision is even more ambitious: a sensor-driven, automated “lightless factory” operating autonomously on-site.
Construction in the factory
In contrast, the DPTA model (Design, Prefabricate, Transport, Assemble) moves construction into the factory, especially for mechanical, electrical, and plumbing (MEP) systems.
Each module is designed digitally using BIM tools like Revit, MagiCAD, and Solibri, ensuring precise coordination, clash detection, and logistics planning. Once fabricated, these modules, some weighing up to 8 tons, are shipped to the site and assembled with minimal adjustment, much like Lego blocks.
The CSCEC 3rd Bureau has applied the DPTA approach to over 200 projects, including subway systems, offices, and high-rises. It brings measurable gains in speed, cost-efficiency, quality, and sustainability, while reducing on-site disruption.
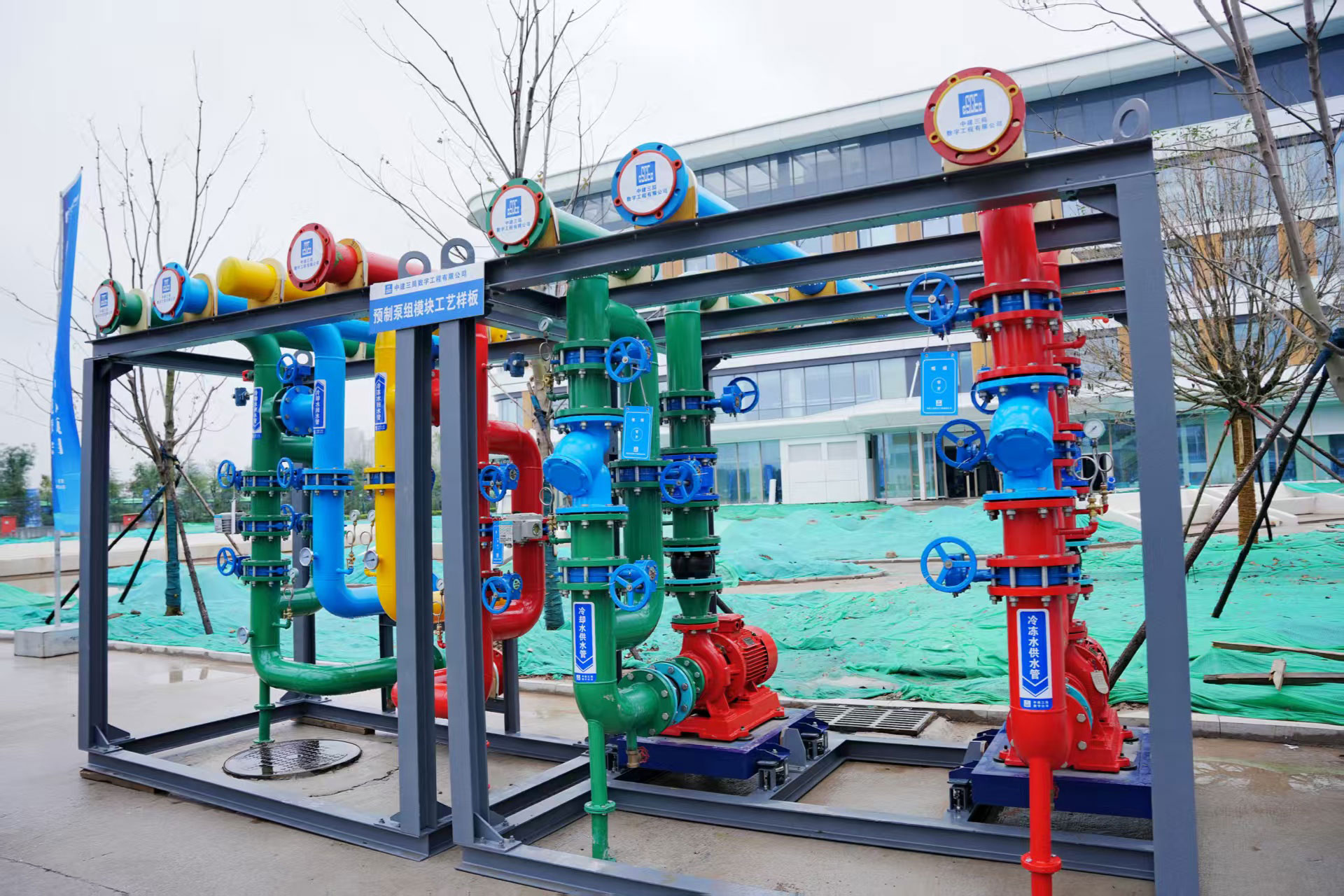
The enablers of industrialization
These strategies reveal that industrialization doesn’t mean a one-size-fits-all solution. Some projects will benefit more from offsite modularization, while others from site-based automation. But both approaches share a common foundation: digital-first thinking, standardized processes, and tight integration.
The success of these innovations is also due to organizational structure. The China Construction Third Engineering Bureau vertically integrates design, manufacturing, and construction, which streamlines execution and fosters continuous innovation.
Scaling up
These models provide valuable lessons as global construction faces increasing demands for productivity, sustainability, and speed. However, one should not expect any innovation to succeed in isolation. They must be incorporated into project planning as early as possible, and have a supply chain capable of delivering the required quality on time and budget.
Read my interview at AEC-Business.com.
View the original article and our Inspiration here
Leave a Reply