I recently spoke with the CEO of a mechanical contractor and asked whether their installation teams are already using BIM models. “Every day,” he responded. “They want to check the placement of ducts and other components on a 3D model before starting the installation.”
That’s just one example of how Building Information Modeling impacts construction workflows. There are many other ways BIM can and already is making construction more efficient, reducing risks, and improving quality and safety for contractors.
Drawings Still Dominate
Architects and other designers have touted BIM since the early 2000s, but contractors’ primary use of design information has been 2D drawings on paper or PDF files. A CEO of an MEP consulting firm went so far as to say that they are still “PDF factories” for the construction industry.
Sticking with the old has made BIM less valuable for contractors. When models are turned into drawings for QTOs, construction, and assembly, the potential value of design data remains untapped.
Fortunately, many clients, contractors, and manufacturers have recognized that BIM goes beyond effectively producing drawings and visualizations. With the right data and integrations, it is the core enabler for industrialized and digitalized construction.
De-Risking Bids with BIM
A bid based on facts rather than assumptions forms a solid foundation for a successful project. Many contractors utilize BIM for quantity takeoffs, particularly if they possess the necessary in-house expertise. BIM accelerates the process and enables the visual verification that all the required parts and materials have been accounted for.
A reliable BIM QTO requires a model that adheres to standards and is free from geometric errors. Unfortunately, that is not always the case, so some contractors have chosen to rebuild the models to comply with their standards. Even in that case, they consider modeling superior to traditional estimation.
Better Coordination and Planning
When all the design disciplines utilize BIM, the age-old dilemma of detecting clashes on the construction site can be alleviated. Designers, BIM managers, and coordinators use model-checking software to ensure the quality of the models and identify conflicting structures and installations.
Hundreds or sometimes thousands of clashes can initially require attention in large projects. If even a fraction of these remained unnoticed, the costs for the designers, contractors, and the client could be substantial. That’s why model checking is critical for everyone.
A relatively recent approach to utilizing BIM involves linking the models to the schedule. 4D BIM requires some initial effort, but it enables more controlled planning, procurement, and construction sequencing. 4D simulation also allows the visual and comprehensible communication of the order and timing of installation.
Some projects use 4D BIM even for design scheduling, which helps both contractors and designers anticipate information needs before they cause delays.
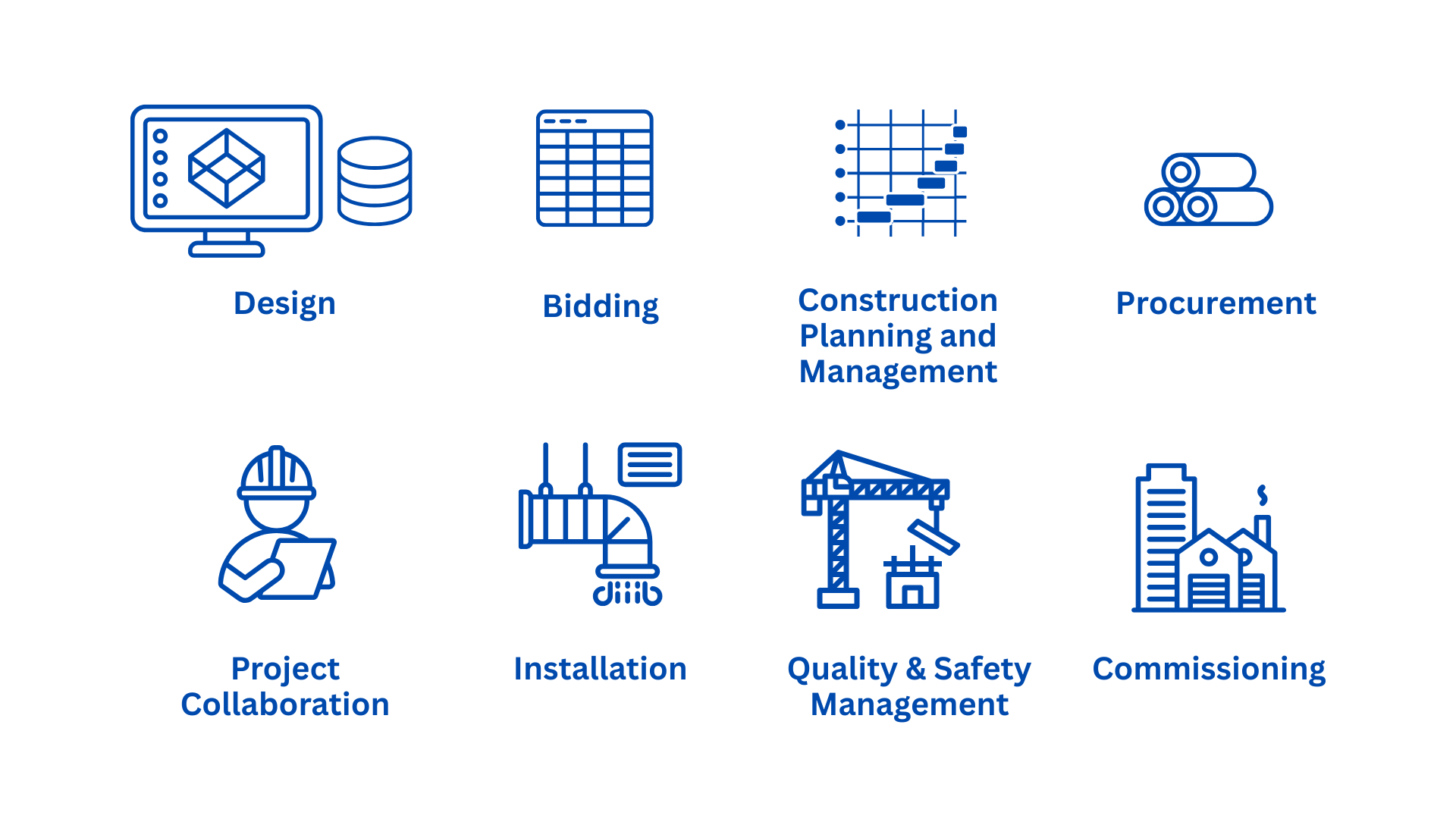
Location-Based Quality Assurance
Due to various reasons, the as-built does not always coincide with the designs. Tools are available to compare the built reality with the BIM models on the construction site. They use photos or 3D scans to document the site. Like clash detection, this practice saves time and money by spotting discrepancies that can lead to a domino effect and costly rework.
A construction project requires a large number of quality inspections and verifications. Software developers face challenges in making this process as smooth and automated as possible. Using BIM Collaboration Format, a buildingSMART standard, they can link comments, issue descriptions, snapshots, viewpoints, and markup with the corresponding element in the BIM model.
Every issue is linked and communicated through a BIM model and routed to the correct recipient, streamlining RFI and inspection workflows and making information available to all parties involved.
The emphasis on accessibility and practical application is precisely what’s needed to move BIM beyond a design exercise and into a truly valuable construction tool. With its integrated BIM viewing, issue tracking, and quality assurance capabilities, solutions like Congrid empower site teams to access and interact with models directly from the field. Critically, these BIM features are built into the tools site teams already know and use daily.
Features like the ability to log observations directly onto the model, measure distances, and view sections of the building make it easier for supervisors and quality managers to make informed decisions, resolve conflicts quickly, and streamline communication with designers and engineers.
By linking the virtual world of BIM with the real-world conditions of the construction site, we can finally realize the full potential of this transformative technology.
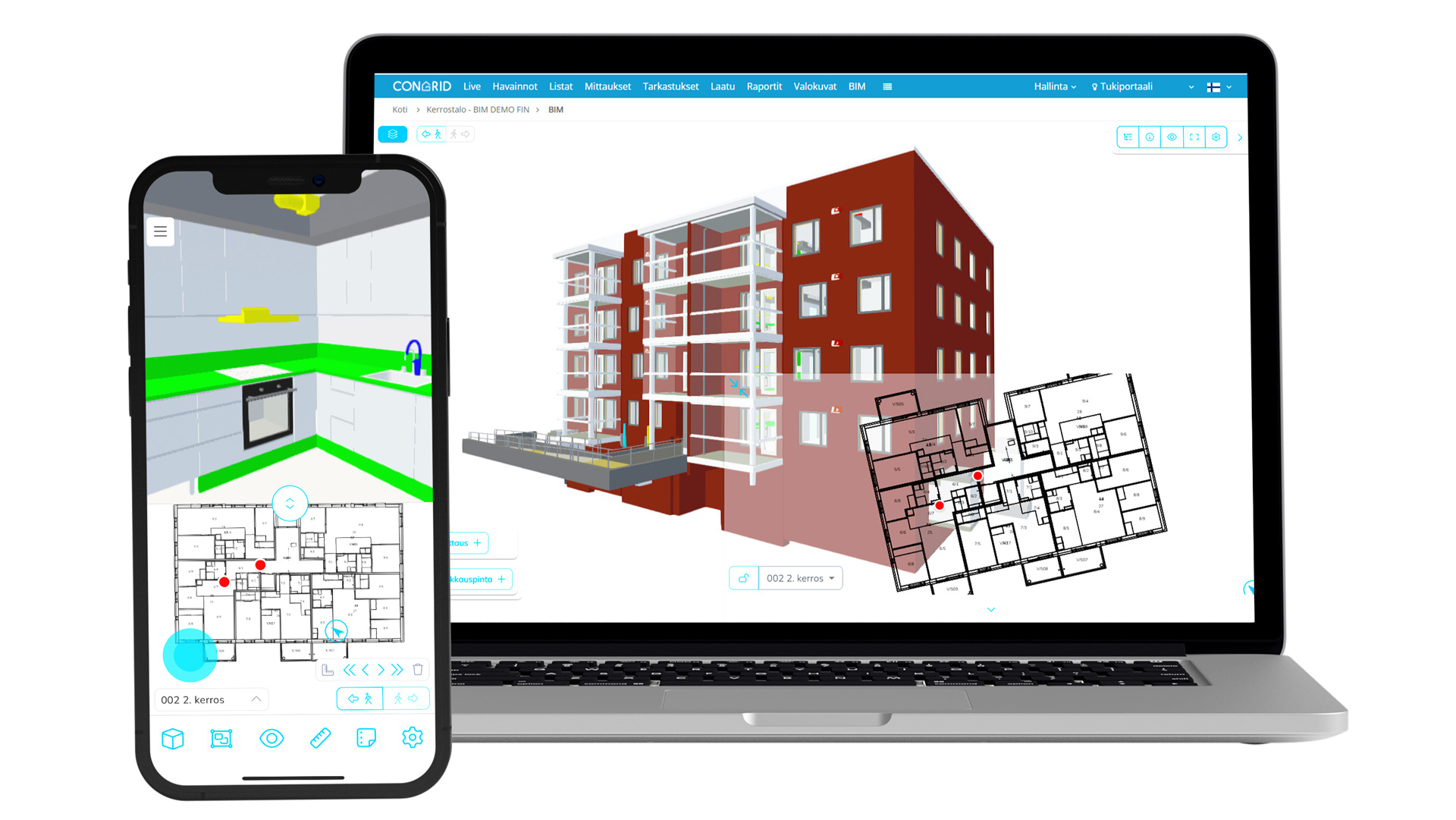
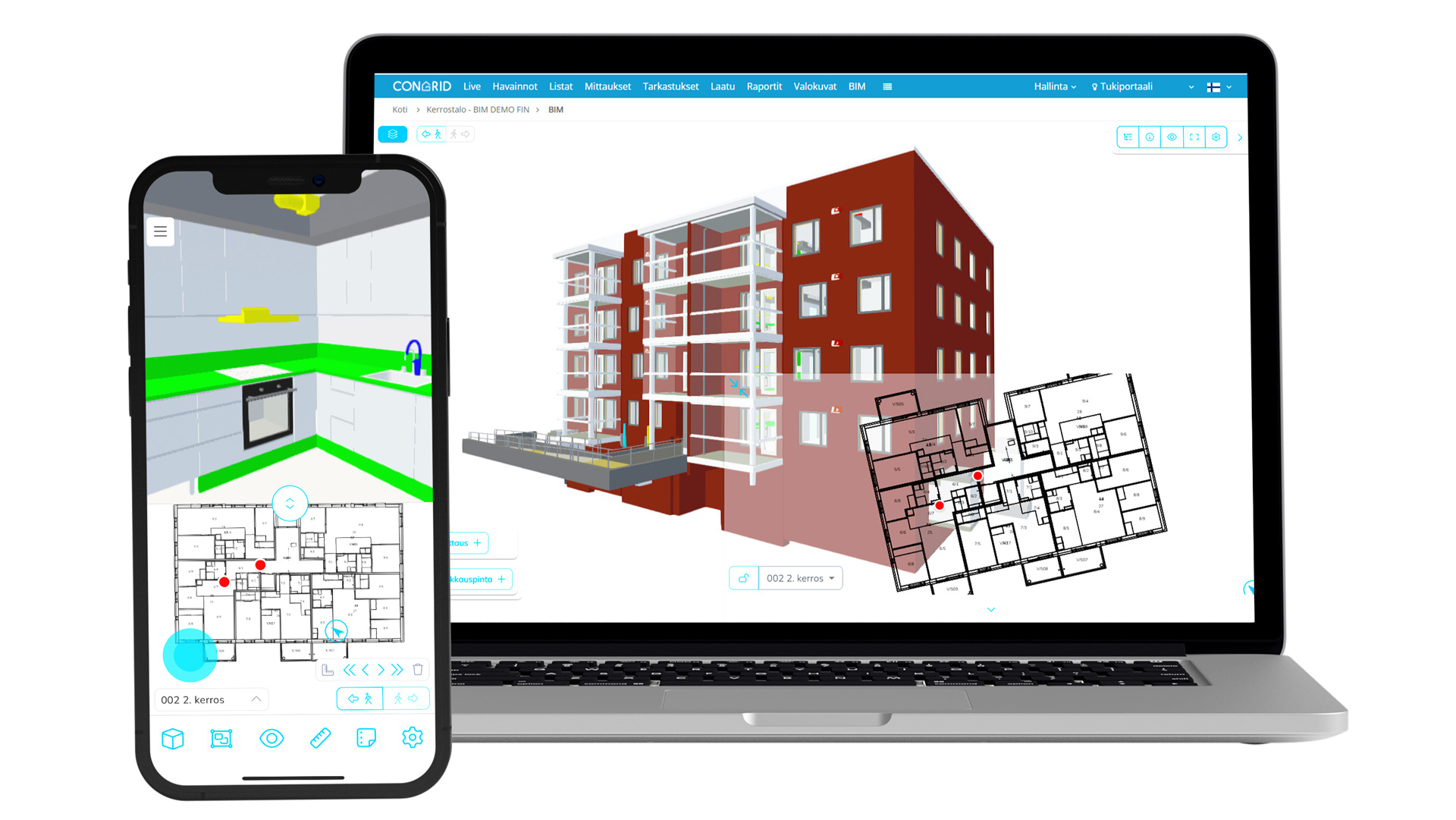
Constructible Designs
Designers determine how various installations are done, even when they lack the practical knowledge to make informed decisions. Installation workers may not respect the design and hence improvise the placement and installation order of components on the site. That can lead to unexpected consequences.
BIM provides a virtual environment for designers and contractors to collaborate and ensure the constructability of designs. IPD projects have demonstrated the power of BIM collaboration in a Common Data Environment. The designs are optimized for manufacturing and assembly, which reduces costs and speeds up construction.
Industrializing Construction Sustainably
For decades, manufacturers have used Product Data Management (PDM) to organize, track, and control all information related to a product throughout its lifecycle. This includes digital models, specifications, Bills of Materials, revisions, workflows, and documentation. PDM breaks down silos between engineering, manufacturing, and procurement. The construction sector can and should learn from manufacturing to become more efficient and industrialized.
According to recent studies, the same product information is created and recalculated at least six times in a typical construction project, and the results are different in every iteration. Contractors and designers save hundreds of hours of unnecessary work when a project has a consistent, model-based PDM process.
Another driver for improved data management is regulation. Contractors must comply with the EU’s and other regulators’ sustainability reporting requirements. With BIM, linked databases, and EPDs (Environmental Product Declarations), environmental assessments become more reliable, transparent, and faster to produce than by using drawings and spreadsheets.
Another regulatory demand is accelerating BIM implementation. Governments in Finland and other countries with high BIM maturity are mandating the use of BIM in building permits. Many public sector building owners view this as an accelerator for the “golden thread” of building lifecycle information discussed in the UK.
Serving the on-site workers
The ultimate construction performance metric is how much value-adding work an individual or team can complete during the workday. Aalto University’s and other studies have shown that installation workers spend around 20% of their time on actual installation. The rest consists of preparatory tasks, information search, material hauling, etc.
Innovative construction firms have demonstrated that project lead time can be reduced by up to 45% with BIM-based information management, integrated material logistics, and Takt production without sacrificing quality or worker well-being. They have reduced project waste and created an environment where an individual worker’s productivity is more than double that of a traditional project.
Safety is another worker concern in construction. Unlike factories, construction sites are constantly changing. BIM is a valuable technology for planning safety barriers, scaffolding, and other safety features as the work progresses.
Next steps and the future
Implementing BIM is not a project but a journey. Luckily, you don’t have to be a BIM expert to start utilizing it, as a growing number of tools make the technology accessible to everyone in the construction industry.
To conclude, here are my suggested steps that contractors can take to enhance their business with BIM:
- A good way to begin is by equipping site teams with tools that let them view BIM models, take measurements, plan installations, and report quality or safety issues.
- From there, you can develop in-house expertise to extract quantities and drive procurement workflows from the model.
- Once those foundations are in place, adopting 4D BIM and using the model for project planning and scheduling becomes a natural next step.
This article was written in collaboration with Congrid.
View the original article and our Inspiration here
Leave a Reply