On April 16, 2025, the Dalux User Days in Helsinki provided a refreshing experience. Attendees weren’t bogged down in complaints about poor productivity; instead, leading construction and consulting firms showcased successful digitalization case studies.
Lasse Forss kicked off the presentations by detailing how SRV, a Finnish construction company, leveraged Dalux for inspections in the demanding Jorvi hospital project.
A Demanding Project
The Helsinki and Uusimaa Hospital District (HUS) commissioned a significant expansion of Jorvi Hospital in Espoo, Finland. The project involves constructing a new ward building with a gross floor area of approximately 50,000 square meters (540,000 square feet).
Executed using the alliance model, the project emphasizes collaboration between the client, designers, and contractors. Construction began in early 2023, and the new ward building is expected to be commissioned in 2026.
Almost 7,000 Internal Handovers
Lasse Forss, a project engineer, introduced Dalux for managing quality inspections and “internal handovers.”
An internal handover is a pre-final inspection phase where the construction company or subcontractor inspects completed work internally to its quality assurance or commissioning team before the official handover. This process ensures everything meets quality and contractual requirements.
Lasse emphasized that implementing a new digital process must be purpose-driven to succeed. In this case, the digitalization of inspection was crucial due to the project’s complexity and the sheer volume of nearly 7,000 internal handovers.
A BIM-Powered Process
Dalux is recognized for its efficient BIM Viewer, which is available for free on mobile and desktop devices. Dalux Field, a paid app, facilitates creating, assigning, and tracking quality and other issues on the jobsite.
Dalux offers a straightforward process for creating forms for internal handovers, streamlining inspections of elements like door hardware installations. The Dalux mobile app lets users record inspections and punch lists with location-based tagging.
Inspection points can be added manually via the desktop app or imported from Excel. Lasse Forss explained his methodology for using Dalux to create BIM object groups for inspection.
Extensive Use
Dalux became a critical inspection tool, with 211 user groups and over 1,100 users actively utilizing the app.
Subcontractors, initially accustomed to Excel or other internal tools, readily adopted Dalux. They experienced time savings and accelerated invoicing for completed tasks.
The visual representation of inspection points and their statuses on a floor plan proved to be a significant advantage over traditional Excel checklists; consider the complexity of managing 800 room sensor inspections without visual aids.
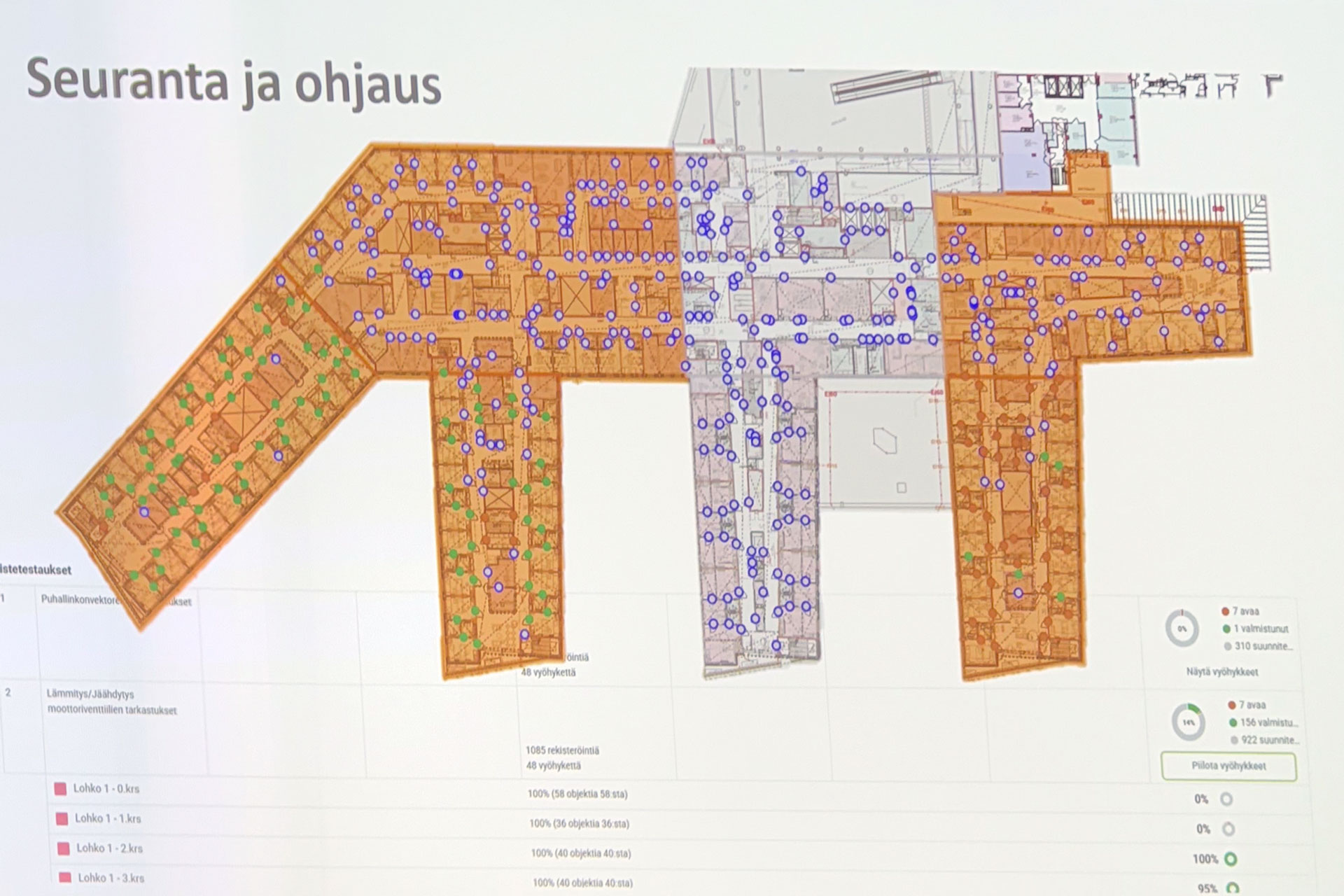
Observations and Challenges
Network connectivity posed a challenge at the Jorvi site, a common issue in construction. Digital workflows are inherently vulnerable to network disruptions, though this issue was eventually resolved at Jorvi.
The implementation of Dalux led to more meticulous inspection planning, enhancing on-site inspection speed but demanding more upfront preparation.
Lasse Forss pointed out that utilizing BIM for quantity takeoffs and inspection planning immediately exposes model errors or omissions, underscoring the importance of maintaining BIM quality throughout the project lifecycle.
Serving the Building Life Cycle
Maintaining an as-built record of each component’s data and inspections yields substantial benefits for the owner throughout the building’s life cycle. This is particularly critical for highly technical facilities like hospitals, where the absence of such data would be a major disadvantage.
Customer feedback from the Dalux User Days was overwhelmingly positive, indicating that the company has successfully developed user-friendly and rapidly implementable tools. This is crucial for construction projects involving various stakeholders with differing levels of technological proficiency.
View the original article and our Inspiration here
Leave a Reply